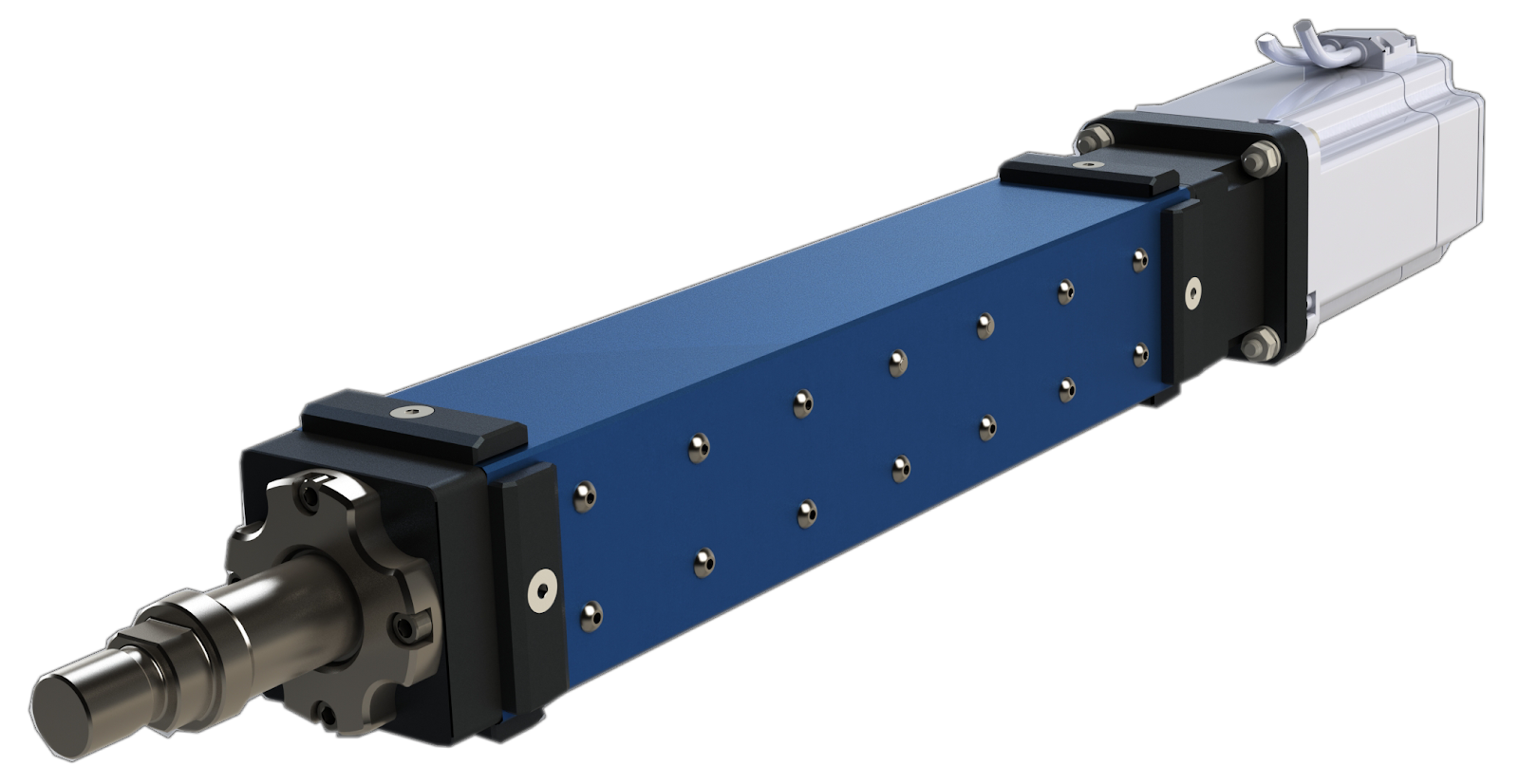
By Brian McMorris
Recently a Futura-Automation customer expressed a problem with Vortex gate valves on an outdoor metal chip collection system getting stuck. The gate valves are mounted on a vacuum system. The factory operates an “air-lock” that maintains vacuum when the collection system is emptied into a bin.
Normally, the plant-side valve is open and the outdoor bin-side valve is closed allowing chips to be pneumatically transported and collected in the collection system hopper, similar to that from National Conveyor Systems. Once the hopper becomes full, the plant-side valve is closed and then the outdoor bin-side valve is opened to empty the hopper into the bin while maintaining plant-side vacuum against the closed valve.
The OEM gate valve is operated by a pneumatic cylinder, the traditional approach to gate valve operation. But in this plant is in a
location with cold winter months. Occasionally the moisture in the pneumatic line frosts up restricting flow to the point the valve will not move. This creates a significant maintenance problem that is difficult to repair, requiring heat applied to the air supply lines to the cylinder.
The customer called on Futura Automation through its local distributor to solve the problem. It was decided to use an LPD electrical linear actuator from Creative Motion Controls (CMC) of Woodinville, Washington. This line of actuators very efficiently converts rotary force from an electric motor to a mechanical roller screw incorporating the patented “grooved roller screw thrust bearing” from CMC. This design allows for a smaller actuator for the force applied, making this a great choice to retrofit existing gate valves operated by pneumatic cylinders.
Many factories that process ag products, food, wood, metal and plastic collect dust or other bulk solid debris from the manufacturing process and dispose of the waste in an environmentally beneficial way. Utilizing the LPD250 will reduce downtime for the chip handling system and simplify maintenance.
Recent Comments