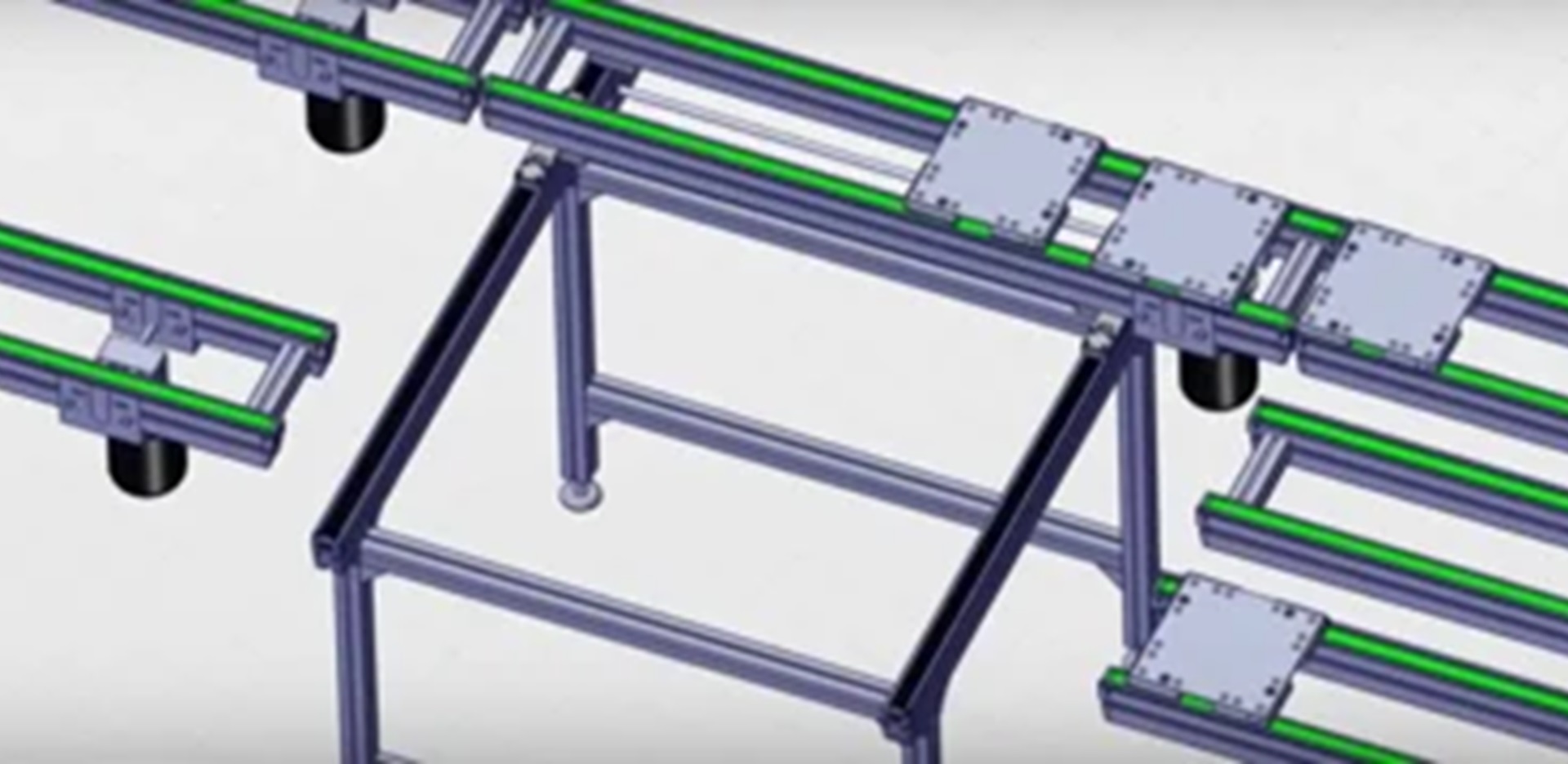
April 19, 2024
Production systems for automated assembly manufacturing will require conveyance of parts from one assembly station to the next. There are many ways to accomplish this task with varying repeatability and speed and resultant cost. Among the myriad conveyor techniques, multi-strand conveyors stand out for their versatility and robustness. Within this category, two prominent types dominate the landscape: timing belt conveyors and roller chain conveyors. In this comprehensive exploration, we delve into the intricacies of multi-strand conveyors, dissecting the features, benefits, and applications of each type.
Understanding Multi-Strand Conveyors
Multi-strand conveyors, as the name suggests, utilize multiple strands (also called strings by some) to convey products or materials from one point to another. Materials for assembly can be on a pallet designed to fit the conveyor or lay directly on the strands. The utilization of multiple strands provides several advantages over single-strand (belt) conveyors, including increased load capacity, enhanced stability, and greater flexibility in design and layout.
Timing Belt Conveyors: Precision and Efficiency
Timing belt conveyors employ toothed belts made from polymeric materials such as polyurethane, ensuring precise movement and alignment of products. The teeth on the belt mesh with corresponding sprockets, allowing for smooth and synchronized operation. This design minimizes slippage and ensures accurate positioning, making timing belt conveyors ideal for applications requiring precise indexing and alignment.
One of the key advantages of timing belt conveyors is their ability to handle heavy loads with ease. The multiple strands distribute the load evenly, reducing stress on individual components and enhancing overall system reliability. Additionally, timing belt conveyors offer low maintenance requirements and minimal downtime, thanks to their durable construction and efficient power transmission.
In terms of applications, timing belt conveyors find widespread use in industries where precision and efficiency are paramount. From automotive assembly lines to medical device to electronics manufacturing, these conveyors excel in transporting delicate components and products with high accuracy and repeatability. Their ability to operate at high speeds further enhances productivity, making them indispensable in fast-paced production environments.
Roller Chain Conveyors: Durability and Versatility
Roller chain conveyors, on the other hand, rely on chains with rollers to convey materials along the conveyor path. These chains are driven by sprockets, providing robust and reliable power transmission. Roller chain conveyors are renowned for their durability and versatility, making them suitable for a wide range of applications across various industries.
One of the primary advantages of roller chain conveyors is their ability to handle heavy loads over long distances. The inherent strength of roller chains allows them to withstand high loads, over 1000 lbs in some cases, without sacrificing performance, making them ideal for transporting bulky and cumbersome materials like automotive sub-assemblies, appliances and furniture. Additionally, roller chain conveyors offer flexibility in design, allowing for easy customization to suit specific application requirements.
In terms of durability, roller chain conveyors outshine many other conveyor types. The rugged construction of the chains and sprockets ensures long-term reliability, even in harsh operating conditions. With proper maintenance, roller chain conveyors can provide years of trouble-free service, making them a cost-effective solution for material handling needs.
Motorized Power Drives
Both Multi-strand conveyors and Roller Chain conveyors rely some form of locomotion. This is contrasted with gravity roller conveyors which require no locomotion. To achieve the repeatability desired in automated assembly, roller-chain and multi-strand conveyors utilize “fractional” DC motors that can be serially controlled to operate in zones. A zone can be just a little more than the length of the product or the pallet to achieve “Zero Pressure” conveyance, with no contact between adjacent pallets or product when directly conveyed.
Such small DC motors are synchronized and controlled by a serial network connection using a variety of “bus” protocols, including Ethernet IP. They also can offer optical encoder feedback so position is always known though the inherent slippage of a pallet on a multi-strand conveyors makes precise position of each pallet unknowable. A wireless RFID tag and regular readers along the conveyor could be employed on each pallet so location of the pallet is always known. Physical “stops” are also deployed on many conveyor systems to block a pallet or directly conveyed product from proceeding, even if the conveyor continues to operate. These are used for flow control at intersections where conveyors cross or change direction at right angles by a “Lift and Turn” mechanism.
Vertical Conveyance and Transfer Units
Some manufacturers offer vertical conveyance which is similar to an elevator. The pallet or product is conveyed into a section that has a vertical conveyor drive and will move the pallet or product to a different level in the system. This can be used for conveyance in a compact floor area, for “over-under” product redirection, for product buffering or for warehousing the product on multiple levels
Comparative Analysis: Timing Belt vs. Roller Chain
While both timing belt and roller chain conveyors offer unique benefits, choosing between the two depends on various factors, including application requirements, environmental conditions, and budget constraints.
Precision and Accuracy: Timing belt conveyors excel in applications requiring precise positioning and synchronization, thanks to their toothed belt design. They are ideal for tasks such as indexing, sorting, and assembly, where accuracy is paramount.
Load Capacity: Roller chain conveyors boast superior load-carrying capacity, making them suitable for transporting heavy materials and products over long distances. Their robust construction and ability to withstand high loads make them a preferred choice in industries such as mining, construction, and logistics.
Maintenance Requirements: Timing belt conveyors typically require less maintenance compared to roller chain conveyors. The absence of lubrication requirements and the simplicity of belt replacement contribute to lower maintenance costs and reduced downtime.
Flexibility: Roller chain conveyors offer greater flexibility in terms of layout and design. Their modular construction allows for easy customization and adaptation to changing production needs. Additionally, roller chain conveyors can accommodate inclines, declines, and curves, making them suitable for complex material handling scenarios.
Cost Considerations: While timing belt conveyors may have lower upfront costs, roller chain conveyors offer better long-term value due to their durability and longevity. The total cost of ownership, including maintenance and operational expenses, should be factored in when making a decision.
Applications and Industries
Both timing belt and roller chain conveyors find applications across a wide range of industries, including automotive, food and beverage, packaging, and logistics.
Timing belt conveyors are commonly used in:
- Electronics and solar manufacturing
- Medical Device production
- Pharmaceutical production
- Precision engineering
- Cleanroom environments
Roller chain conveyors are prevalent in:
- Warehousing and distribution
- Automotive manufacturing
- Appliance manufacturing
- Heavy-duty manufacturing
- Mining and aggregates
- Timber processing
Conclusion
In conclusion, multi-strand conveyors, whether timing belt or roller chain, offer an array of benefits and applications in the realm of material handling and automation. While timing belt conveyors excel in precision and efficiency, roller chain conveyors prioritize durability and versatility. Understanding the specific requirements of each application is essential in selecting the most suitable conveyor type. By leveraging the strengths of timing belt and roller chain conveyors, industries can optimize their material handling processes and enhance overall productivity and efficiency.
Recent Comments