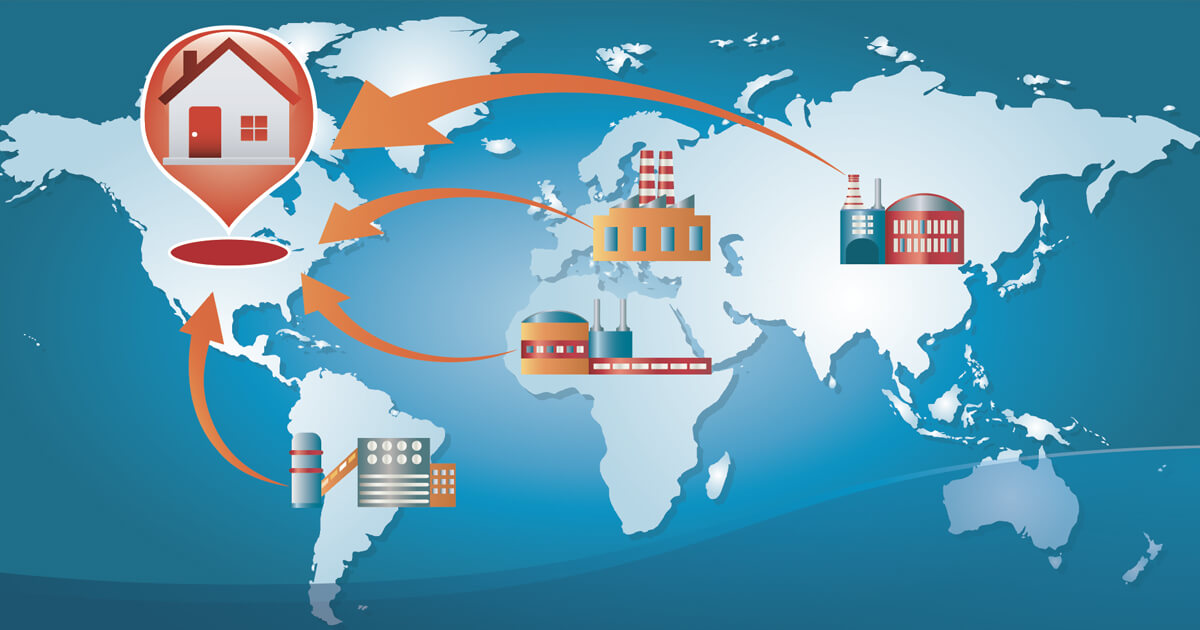
POSTED 07/03/2024 | By: Carrine Greason, A3 Contributing Editor
Reshoring is gaining momentum — a lot of it. Manufacturers are rapidly bringing production back to the United States from overseas or at least closer to home in a related move called nearshoring. Both reshoring and foreign direct investment have grown, from generating 11,000 new U.S.-based jobs per year in 2010 to more than 300,000 in 2022, and another 180,000 jobs recorded in just the first half of 2023. Advances in automation are playing a big role in this phenomenon by helping domestic producers to overcome many of the challenges that drove production offshore in the past.
For decades, low factory prices available from offshore manufacturers led U.S. companies to send work overseas. But in 2020 the COVID-19 pandemic brought global supply chains to a halt and sent workers home. The business response to the public health catastrophe accelerated deployment of automation in North American factories. A variety of U.S. legislation further incentivized domestic manufacturing. As a result, many companies are rethinking the location of their manufacturing footprints.
To learn more about reshoring and nearshoring, including both benefits and challenges, and to understand how advances in automation enable cost-competitive domestic manufacturing, we spoke to automation and reshoring experts at Futura Automation and Reshoring Initiative®.
What is reshoring?
The Reshoring Initiative defines reshoring as “the practice of bringing manufacturing and services back to the U.S. from overseas.” The organization’s website shares that in addition to strengthening the U.S. economy, reshoring benefits domestic companies by reducing the total cost of products and spurring product innovation.
What is nearshoring?
Nearshoring is similar, except that it brings manufacturing not back to the United States, but closer to it. A top factory automation trend of 2024, nearshoring is the relocation of foreign manufacturing or business operations, usually from Asia, to nearby countries or regions, typically close to the company’s base of operations. For U.S. companies, North American countries — Canada, Mexico, and Caribbean nations — are popular nearshoring locations.
Reshoring trends
Mentions by U.S. firms of reshoring, nearshoring, and onshoring — a synonym for reshoring — doubled year over year since the start of 2022, according to data compiled by Bloomberg.
“The first 15 years of my career were more about consolidation: moving manufacturing to Mexico or Asia or to Eastern Europe,” Joe Cutillo, CEO of Sterling Infrastructure — a provider of e-infrastructure, building, and transportation solutions — is quoted in Fortune. “It is truly the first time in my life I’ve seen stuff coming back.”
“Mexico is also booming and has the advantages of an available and enthusiastic workforce,” says Harry Moser, president of Reshoring Initiative, a company that assists manufacturers and suppliers in making sourcing decisions by offering a wealth of data about reshoring as well as free analytical tools and resources. Mexico has exceeded China as the source of the most imports to the United States. In addition, Canada posted moderate increases in manufacturing sales and inventories in 2023.
BBC reporter Faisal Islam likens the growth in U.S. domestic manufacturing to developments in China when the country was the fastest growing economy in the world. Based on a recent visit to the U.S. state of Georgia, he writes, “The boom is visible on the ground…. In 20 years of reporting around the world, what I have seen in the U.S. over the past year can only compare to what I saw in China in the mid-2000s.”
U.S. government economic policies in the early 2020s leveled the playing field in some industries. The result is a modern-day gold rush, says Moser. He explains that investments in U.S. manufacturing shifted into overdrive after Congress passed the Chips and Science Act, the Inflation Reduction Act (IRA), and the Bipartisan Infrastructure Law. The three bills incentivized a variety of domestic production and infrastructure development, ranging from silicon chips and clean energy to railways and ports.
Why businesses bring manufacturing home or near home
Supply chain concerns, consumer demand, and total cost of goods are some of the reasons U.S. companies choose to manufacture products at home or closer to home. Moser says lower total cost of ownership (TCO) is a key reason why companies now choose domestic manufacturing. Reshoring and nearshoring often pencil out even when the price leaving a factory in Asia is 30% lower than in the U.S., as demonstrated by the Total Cost of Ownership Estimator®, a free calculator provided by the Reshoring Initiative.
“Sharply rising wages in China, much greater use of manufacturing automation, and new trade policies have reduced the total cost gap between Asian production and nearshoring to almost zero,” reports Supply Chain Digest. Trade policies include tariffs and tax incentives.
A study by Reshoring Initiative reveals that decision-making based on TCO results in U.S.-based manufacturing locales winning against offshoring to China in 32% of the cases, up from 8% when only factory price is considered. The addition of 15% Section 301 tariffs raises the win ratio to 46%.
Moser says that local production also reduces business risk in a world that recently experienced severe supply chain disruptions from a variety of sources: flooding associated with climate change, a ship blocking the Suez Canal, attacks on ships in the Red Sea, and military threats by China against other countries in Asia. “Senior business leaders see reshoring as a form of insurance, like flood or fire insurance, that protects the company against supply chain disruptions that threaten the company’s existence.”
Consumer and corporate interest in environmental and social governance (ESG) also leads companies to produce goods closer to home. U.S. manufacturing achieves a lower environmental impact with factories powered by fuels cleaner than coal, the predominant power source for Chinese manufacturing, and less fuel consumed to transport the goods from the factory to North American consumers.
Other benefits of reshoring and nearshoring include:
- Faster time to market
- Shorter supply chains
- Colocation of engineering and manufacturing personnel
- Lower transportation costs
- Less risk from global instability
- Easier monitoring of product quality
- Less business travel and faster factory acceptance tests (FAT)
- Convenient meeting times that span fewer time zones
- Made in America label
Challenges of reshoring and nearshoring
Manufacturers that choose reshoring or nearshoring have some challenges to meet. One challenge of reshoring may be a lack of manufacturing know-how after decades of offshoring. However, most companies at least build prototypes in-house, and they can draw upon that expertise, explains Moser.
Reshoring challenges may also include higher labor costs and the lack of availability of a skilled workforce. Companies may require skillsets, such as welding and other hands-on crafts, that are less readily available in a new location. Fortunately, automation helps to overcome these challenges.
Best practices in automation spur reshoring and nearshoring
Automation helps to make reshoring and nearshoring not only possible but also cost-competitive in the global marketplace. AI and automation also make manufacturing jobs more enjoyable and can turn manual labor into knowledge work.
Two best practices in automation can significantly reduce the cost of engineering, which in turn lowers total project cost, shortens time to value, and improves ROI: modularized robotics and off-the-shelf automation solutions. Unlike custom-engineered solutions, off-the-shelf solutions reduce risk and lower costs for customers. They also deliver better margins to system integrators, says Brian McMorris, president of Futura Automation, a solutions provider of industrial robot systems, advanced automation, and industrial internet of things (IIoT) systems to North American manufacturers. “Palletizing is a good example of off-the-shelf tools that reduce cost. In general, extending a canned solution produces a lower cost of entry than engineering your own.”
It helps to take a long view. McMorris notes that a robot is a capital investment that can deliver value for 10 years. Accordingly, he recommends that manufacturers target a three-to-five-year ROI. He explains that a robot arm itself constitutes about 25% of the initial project investment. By contrast, approximately 75% is engineering and ancillary equipment. “The best practice is to buy only what you need — select the robot and gripper sized properly for the application, and do not over-engineer. And for engineering, increase the ROI by choosing a well-tested standard solution that minimizes commissioning time as well as initial and recurring engineering costs.”
Advancements enable robots and cobots today to perform assembly work and other highly dexterous tasks that formerly drove manufacturing to lower-wage countries. McMorris goes on to explain, “An automated solution that oscillates parts to singulate, or isolate, individual parts on a flat plate enables a robot to pick up items while using a lower-cost, simpler to teach 2D vision system, instead of a sophisticated 3D AI vision system.”
3D AI vision tools are available for locating in a bin or tray randomly oriented parts that cannot be easily singulated — spongy, rubbery, and sticky parts as well as parts that are too large for a flex feeder, he says. Artificial intelligence (AI) algorithms determine which part is the best to pick and how to pick it based on its pose, such as at a right angle.
Ready-to-use, electronic, ethernet and sensor-integrated gripping technologies, with force feedback in some cases, are an advancement that enables robots and cobots to perform more challenging tasks than previously, such as picking up flexible O-rings. A manipulator goes through the middle of the ring and expands to pick it up, and then an extractor pushes it to place the ring. “It would have cost a manufacturer I worked with $100,000 or more to engineer a custom O-ring gripper in-house,” McMorris says. “Instead, we sourced a commercially available gripper for a wide range of O-ring sizes—from 4mm to 300mm.”
Once a decision is made to produce a component or product domestically, all the subcategories of production are brought home as well, he says. Such tasks include dispensing adhesive, bolting, brazing, cable tying, clinching, crimping, inserting, fastening, finishing, nailing, pressing, riveting, screwdriving, soldering, staking, stapling, and welding. Fortunately, automated and robotic solutions are available for all these assembly tasks as well as for process tasks, such as machine tending, 3D printing, and painting. Advances in robotic welding enable fixed torches and flexible relocation of robot and torch that can autonomously adjust to variances, even after deployment, he adds.
Material handling is another area of automation and robotic innovation that lowers labor costs. Palletizers, conveyors, gantries, autonomous guided vehicles (AGVs), and autonomous mobile robots (AMRs) move parts and supplies around a factory in ways that require less labor.
The future of automation in reshoring and nearshoring
Some tasks remain out of the reach of robots. While technological solutions to fabric cutting and sewing are well known, handling fabric is a new frontier, McMorris says. When robots or autonomous systems master this task, AI may help to create on-demand, one-of-a-kind apparel. Home and shipbuilding are other areas of research in manufacturing automation.
That said, manufacturing automation will continue to play a major role in reshoring and nearshoring because company leaders need to manage risks and total costs. Awareness of global risks has grown while financial incentives and automation have made North American manufacturing competitive again.
Recent Comments