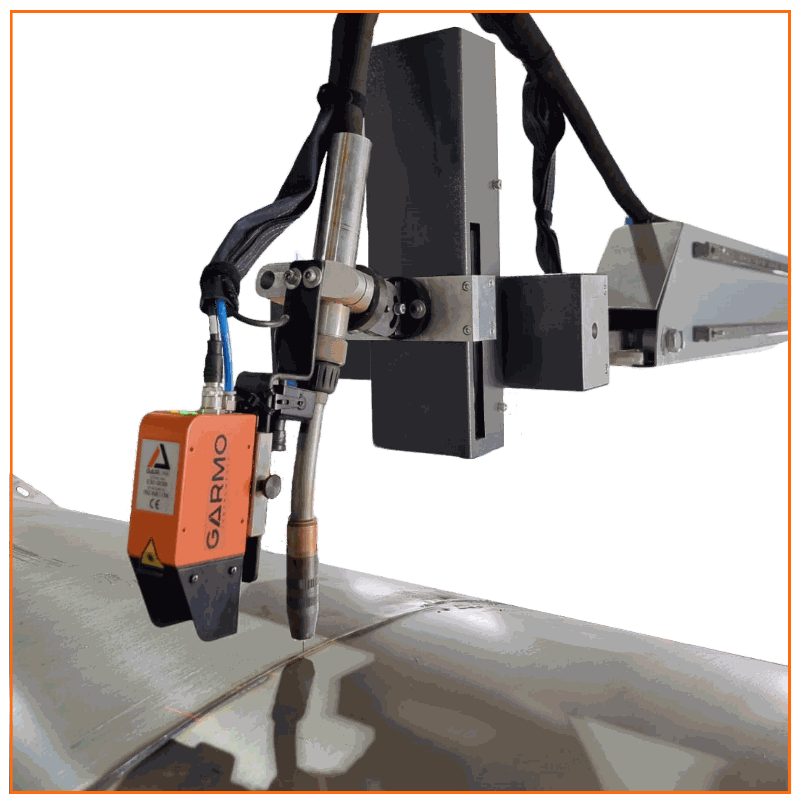
“Autonomous Welding” is the use of robots and AI software to track a pre-programmed welding task and make adjustments to that program dynamically as conditions change. While automobiles require welding of the chassis and body parts, the volumes of a given model produced are very high and so the parts requiring welding can be precisely fixtured and the weld follow a pre-planned path. But for lower volume and often much large parts requiring welding for transportation, precise fixturing / tooling increases production cost and reduces profits. For trucks, train cars, pipelines and ships, a more adaptable, less precise fixturing is desirable. To accomplish that with automation requires autonomous welding solutions.
In the ever-evolving landscape of automated and robotic manufacturing, efficiency and reduced trained labor requirements, quality and precision play pivotal roles in ensuring the success of various industries. One area where this is particularly crucial is in the transportation industries, especially in large scale ship-building, train tank car manufacturing, truck trailer production, and pipeline pipe fabrication. The integration of advanced technologies, such as Weld Seam Tracking using laser line projection, has proven to be a game-changer in enhancing productivity, saving labor cost and improving quality in these sectors. Weld Seam Tracking does not plan the path for the robot held welding torch. Instead, it “course corrects” the torch to match the real-world metal pieces to be welded from their idealized path plan, whether that path was hand-taught by an operator, was programmed between “way-points” or is generated by design and simulation tools such as Octopuz or RoboDK..
Weld Seam Tracking Overview:
Weld Seam Tracking utilizing a laser line profiler is an innovative technology that combines the accuracy of laser tracking systems to control robot movements dynamically with the versatility of Metal Inert Gas (MIG) welding. This system utilizes a laser line projected onto the workpiece, creating a reference line for the welding process and providing robot coordinates to the robot controller dynamically, at 40 coordinates per second sent to the robot controller via one gigabyte socket service ethernet connection (also known as GigE communications). The welding torch is equipped with a laser line profiling sensor that continuously tracks the position and profile of the weld seam, ensuring precise and consistent welding. It is possible to accomplish multiple passes on the same workpiece and also provide weaving or stitching algorithms for wide or varying seam widths for a number of different weld profiles.
Benefits of Autonomous Welding in Shipbuilding:
Shipbuilding is a complex process that demands high precision and efficiency. Laser Line MIG Weld Seam Tracking significantly reduces the risk of errors by ensuring that the welding torch follows the exact path of the seam. This not only enhances the structural integrity of the ship but also accelerates the welding process, leading to faster production cycles at lower cost.
Train Tank Car Manufacturing Advancements:
In the manufacturing of train tank cars, where safety and durability are paramount, Weld Seam Tracking contributes to the production of flawless welds. The technology minimizes the chances of defects and improves the overall quality of welds, meeting the stringent standards required for transporting hazardous materials through population centers.
Revolutionizing Truck Trailer Production:
Truck trailers endure significant stress during transportation over unpredictable roadbeds, making the quality of welds crucial. Laser Line MIG Weld Seam Tracking ensures uniform and precise welds, reducing the likelihood of weak points in the trailer structure. This not only enhances the durability of the trailers but also streamlines the manufacturing process.
Efficiency in Pipeline Pipe Fabrication:
The construction of pipelines demands a high level of accuracy to prevent leaks and ensure the integrity of the system. Laser Line MIG Weld Seam Tracking is a valuable tool in pipeline pipe fabrication, enabling welders to achieve consistent and reliable welds. This, in turn, accelerates the installation of pipelines, contributing to overall project efficiency.
Conclusion:
The integration of Weld Seam Tracking technology using laser line projection promises to be a transformative force in the shipbuilding, train tank car manufacturing, truck trailer production, and pipeline pipe fabrication industries. By combining laser precision with MIG welding capabilities, this technology not only enhances the quality of welds but also accelerates production cycles, ultimately boosting productivity across various manufacturing sectors. As industries continue to embrace technological advancements, Weld Seam Tracking stands out as a key innovation driving progress in the world of welding.
Register for our Webinar on February 2, 2024
Futura Automation, LLC and Garmo Instruments. presents Futura Automation’s webinar on Garmo weld seam tracking “Simple Solutions” webinars on February 2, 2024 at 11am EDT. we will present the technology and functionality of Garmo sensors for weld seam tracking.
Check here to register for the Webinar: https://futura-automation.com/webinar430/
If you would like to subscribe to our Newsletter and Webinars click: https://lnkd.in/gHdn_hJ2.
Recent Comments