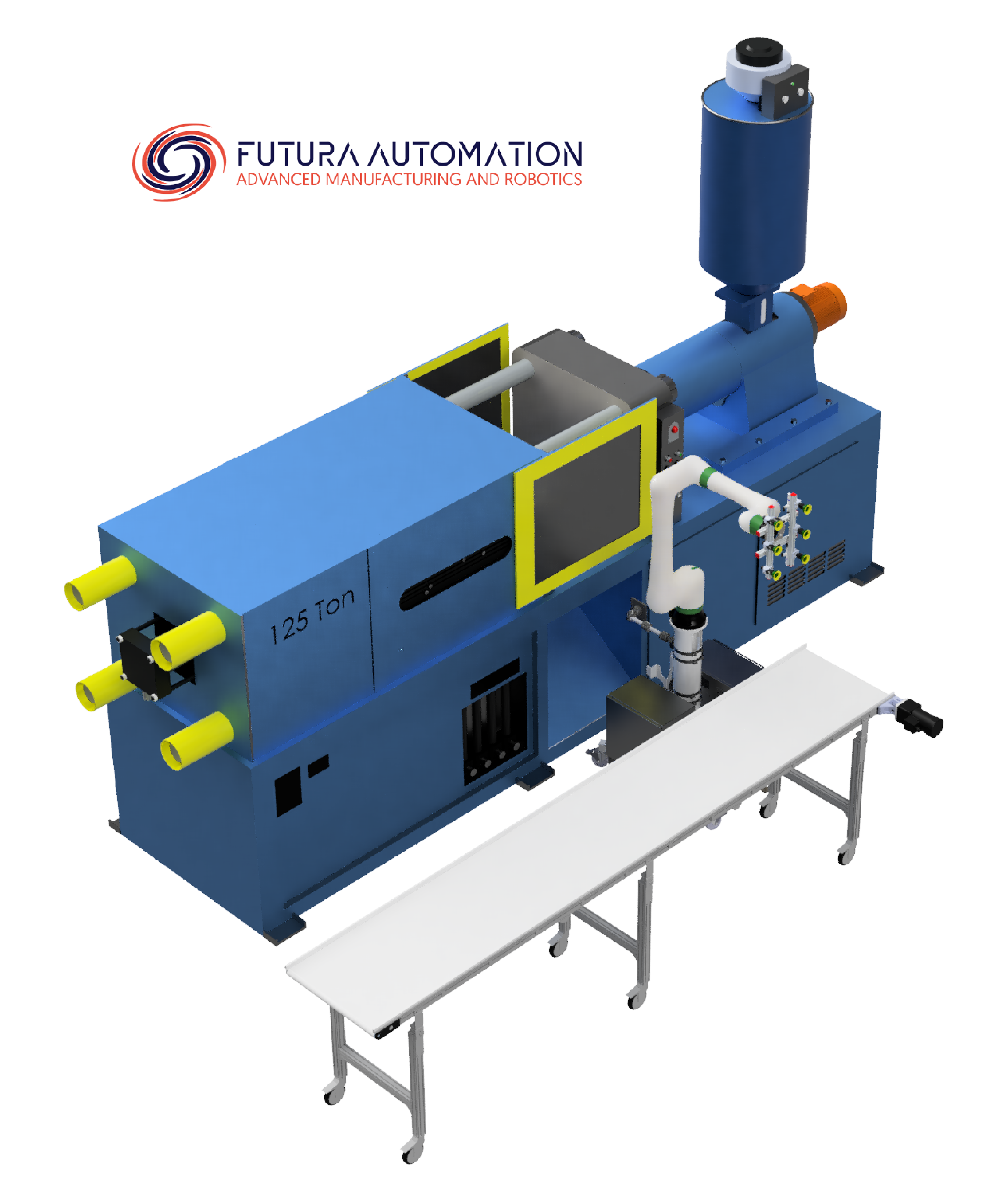
This week’s Simple Solutions features
Injection Molding Automation
Featured Article: How to Plan and Implement Automation in an Injection Molding Plant
Injection Molding Automation:
Industry Best Practices
Before discussing how best to implement automation within your company, let’s quickly help those of you still on the fence to decide whether automation is right for you.
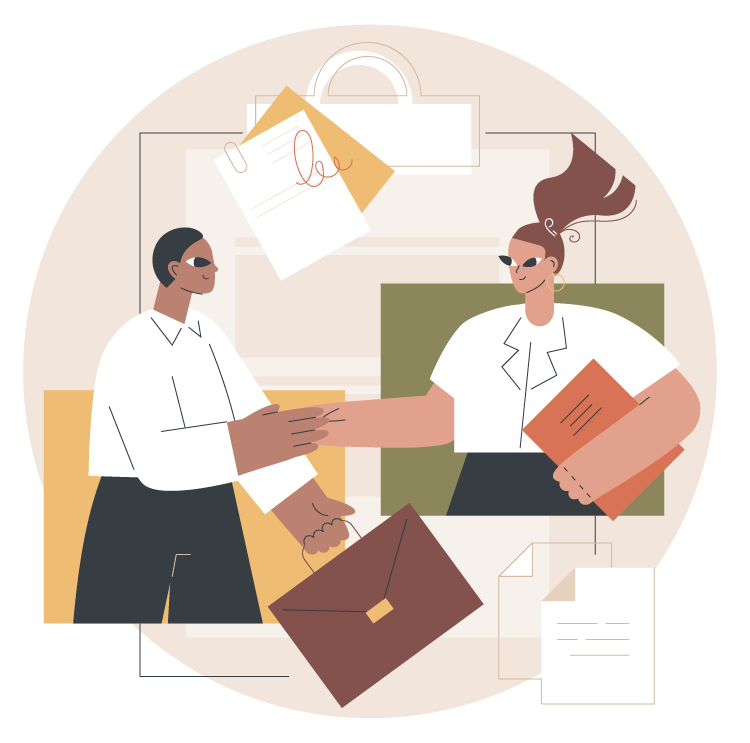
The operators that you already have should be able to get the job done; they just need the right training and support
If you are having a hard time finding skilled operators, process engineers, or maintenance technicians, then automation can almost certainly help you achieve an increase in overall efficiency and quality. Automation almost always works faster and occupies less floor space than a manual operation. Automation systems also do not need breaks and can offer a consistency that manual operation cannot. The added consistency in cycle time not only improves product quality, but also can help you identify more accurate operating costs and production output. Automation can help you to become more successful when competing against other molders.
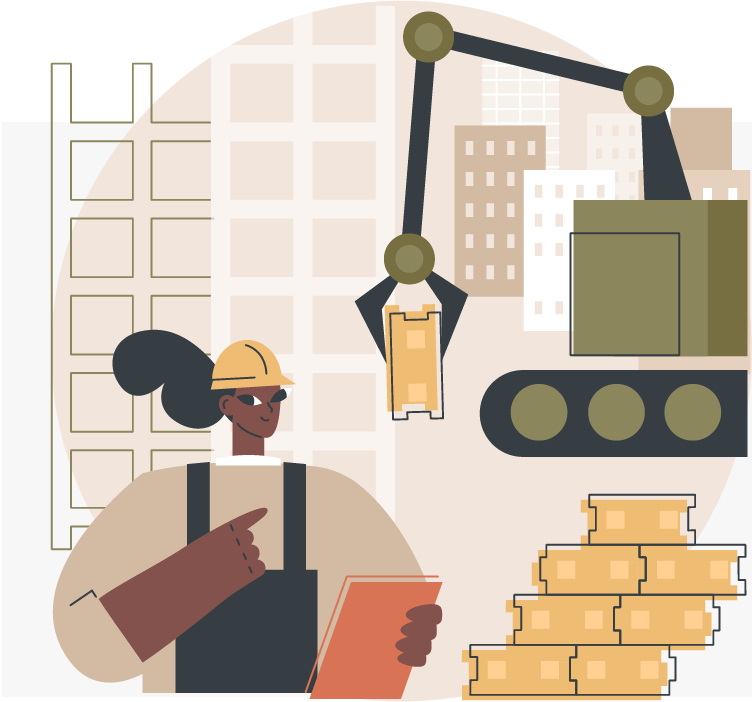
Robots are particularly critical when delicate molded parts need to be handled with care
Automation is an important and necessary step if you are working with parts that have delicate surface features, are comprised of softer materials, and/or have critical dimensions that must be maintained during the molding process. Any uncontrolled interaction with humans can damage a part or decrease its quality. Many medical or high-end electronic parts are particularly susceptible to contamination through human interaction, so automation is essentially a necessity if you are working with products for either of those fields.
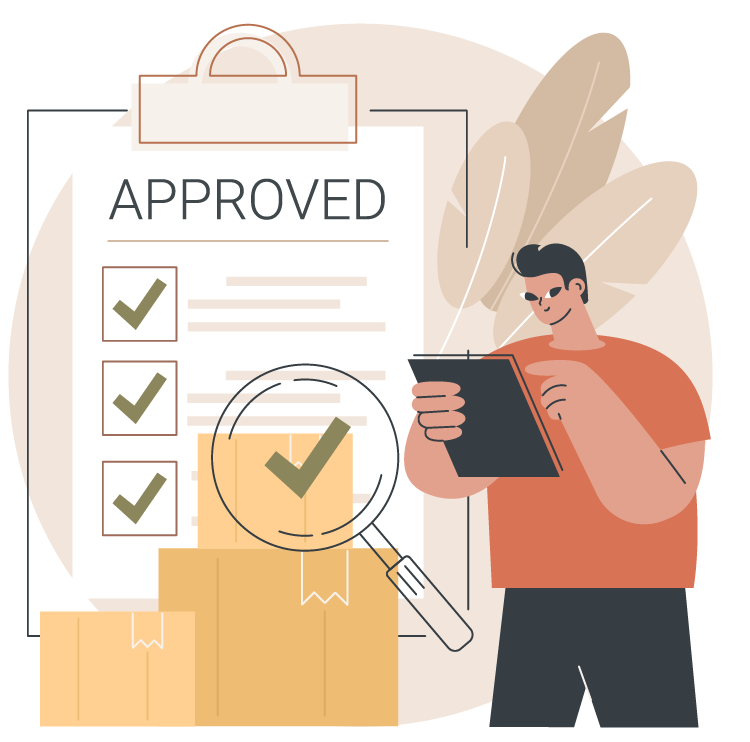
Don’t lose time after every mold change
If the mold is not correctly located, the robot may need to be retaught position points, and adjustments may be required for proper operation. This process can be time-consuming and costly, so it would be wise to minimize the need for it. A servo-wrist option on the robot (instead of pneumatic-type wrists) can certainly help in this effort. In fact, a robot with a servo-driven wrist (also referred to as a five-axis robot) should be considered in any cell for its added flexibility of movement and adjustment.
Join us at the Automate 2022 manufacturing show in Detroit June 6th- 9th and explore Simple Solutions for Injection Molding Automation
Ready Robotics
Kel Guerin, PhD roboticist and CTO and Co-founder of READY Robotics, will explain what No Code programming is, what makes it different from traditional robot programming, and how it can make robots and automation more accessible to all
READY has partnered with an extensive list of automation companies, to ensure that automation components work seamlessly with Forge/OS. We enable control of the entire automation cell by connecting and controlling your automation devices through the easy-to-follow apps preinstalled on Forge/OS. Right out of the box, Forge/OS is compatible with hundreds of robots from the leading brands. With Forge/OS, heavy payload industrial robots are as user-friendly as collaborative robots. Your operators can learn Forge/OS once, and control robots from different brands on a single platform.
Macron Dynamics
Scalable, Economical, Fast: The Advantages of T-Bot and H-Bot Gantries
One of the product lines proudly represented by Futura Automation is Macron Dynamics of Croydon, Pennsylvania. Futura Automation works with our customers and Macron Dynamics to create unique Cartesian or linear robots closely matched to the customer application requirements for an optimal ROI. Macron products are built with the highest quality materials, assembled in the USA, and engineered to withstand the abuses of rigorous, daily usage.
OnRobot
Unique grippers, screwdrivers, force sensors, vision and tactile feedback
OnRobot delivers a full line of plug-and-produce end-of-arm tooling (EoAT) for collaborative and small robot applications. The innovative grippers, sensors, machine vision, tooling and tool changers help manufacturers gain the full advantages of collaborative and lightweight industrial robots, including ease of use, cost-effectiveness, and safety alongside human workers.
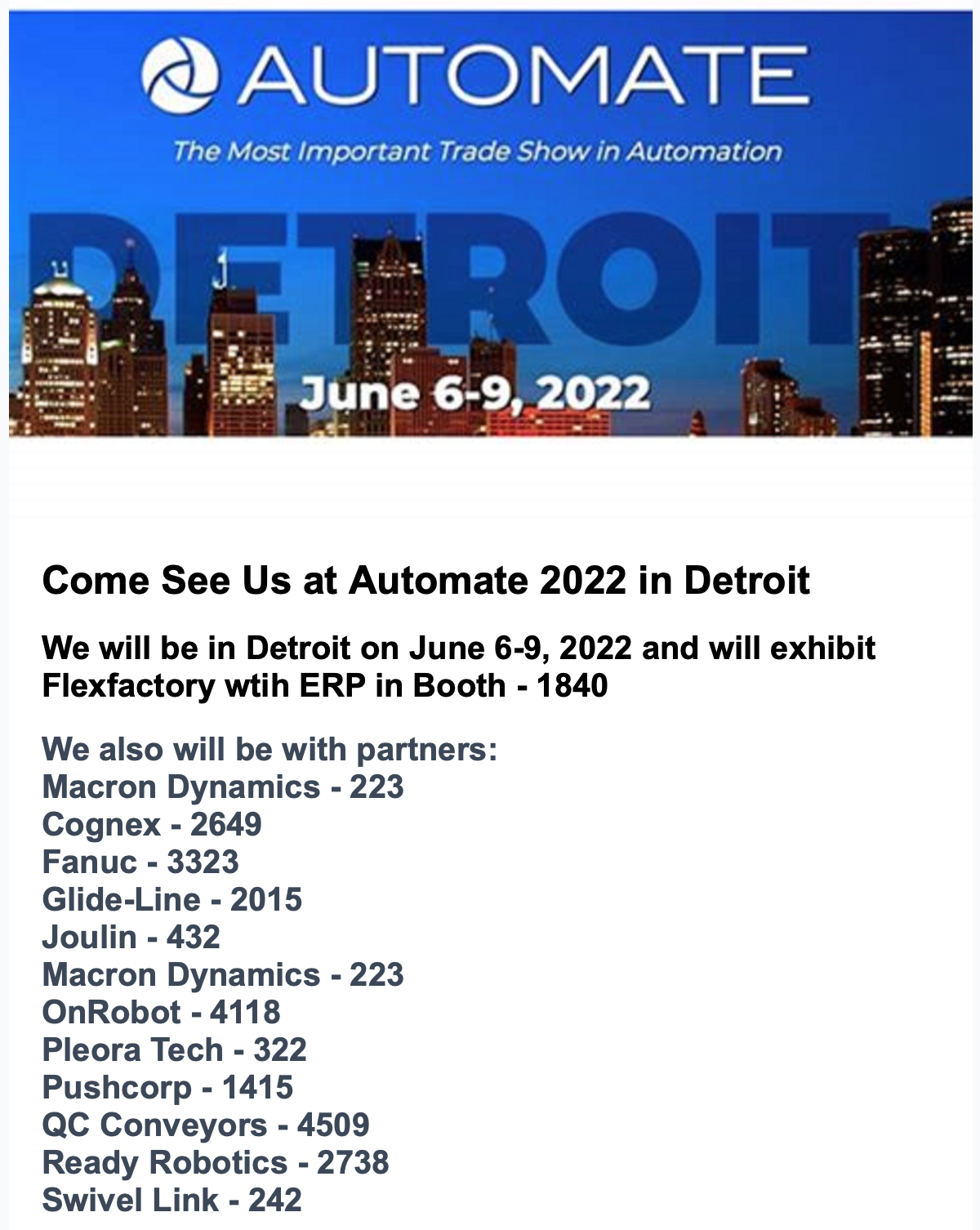
Recent Comments