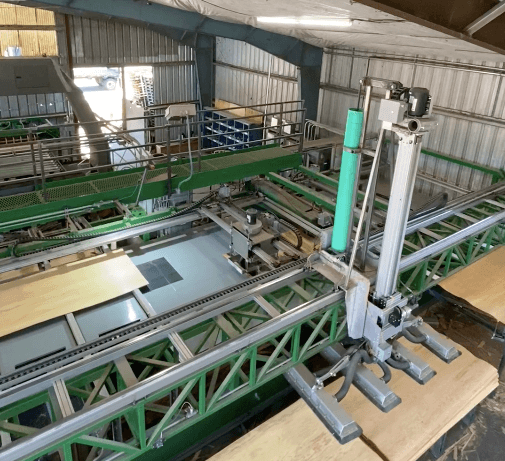
Application: MacBuilt X / Y Dual Systems
Industry: Material Handling & Packaging Automation
Background:
Faced with a legacy system and in search of an automated solution to increase productivity and decrease or eliminate the liability of safety hazards associated with manually operated manufacturing machines for one of their plywood manufacturing clients, OES Automation, a partner company for Futura Autonmation, LLC, turned to Macron Dynamics in support of a more automated solution. Known for its ubiquity as a modern building material, plywood is made up of sheets of veneer which are stacked and glued together. These sheets naturally contain imperfections which are not acceptable on the outside layer according to some plywood grades, so these defects must be identified, removed, and patched.
Key solution goals:
- Increase productivity and operational speeds
- Improve system reliability
- Reduce safety hazards for employees
The Challenge
The client needed a material handling solution that could quickly and precisely position plywood sheets, decrease machine processes throughput times, and eliminate the liabilities associated with lifting heavy payloads over operators.
Key challenges to address:
- Long Z axis travels
- Heavy payloads
- Large moment loads
The Solution:
Working collaboratively with the OES Automation team and their client, the Macron Dynamics Engineering team, supported by Futura Automation, proposed an automated solution in which three multi-axis gantry robots worked in a coordinated motion to efficiently transfer and stack plywood sheets arriving from up-stream veneer cutting and processing:
- Three gantries that move material between:
- Scanning for defects
- Cutting and patching
- Sorting and storage by finished material grade
- 3:1 gear ratio provided via MAC MPG Inline Planetary Gearboxes to deliver optimal acceleration
- Heavy-duty payload and moment loading capabilities
“The system we helped engineer for this customer was a great demonstration of the way we like to work. Our integration experts, engineering team, and the end client collaborated to move from hand-drawn sketches to installed systems that exceeded expectations.” — Syree Berry, Macron Dynamics Application Engineer
GANTRY SPECS AT A GLANCE
Work Cell One: MGS-14X X/Y Gantry System | |
XX-axis Travel: | 8800mm |
YY-axis Travel: | 2675mm |
Max Load: | 25 lbs. |
Work Cell Two: MGS-14X X/Y Gantry System | |
XX-axis Travel: | 3625mm |
YY-axis Travel: | 2675mm |
Max Load: | 25 lbs. |
Work Cell Three: MDS-R20 Dual System | |
XX-axis Travel: | 3625mm |
Z-axis Max Load: | 1,000lbs (tooling and cantilever) |
The Results:
- 100% ROI in six months of operation
- Customer was able to self-install the MACBuilt solution
- Manpower was redeployed to other manufacturing tasks and operations were expanded from one shift to two
- Increased reliability – not a single replacement part was required in the first year of operation
After the MACBuilt system was integrated, the end client was able to replace 8 machines that required a team of 9 operators with one solution that could be managed by one operator. This improvement made it possible to run this system for two shifts, whereas previously it was only possible to run the system for a single shift due to the manpower requirements. This also allowed for the reallocation of manpower to other production tasks, which was doubly beneficial since finding, hiring, and training great employees is difficult and expensive.
The Bottom Line: In only 6 months the client reported that they had seen a complete payback on their initial costs.
“We chose the Macron gantries because of the unlimited amount of travel configurations, good pricing (75% less for the total project) and ease of installation. Macron was very helpful in working with us to get the design we needed. We are approaching a year of operation with the Gantries and they are running great and have been very low maintenance.” — Devin Powell, CEO, OES Automation
Recent Comments