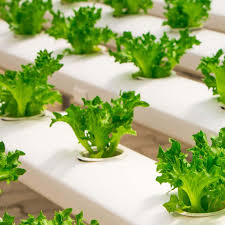
(reprinted with permission of Macron Dynamics)
Background: While the majority of the world’s agricultural and horticultural products are grown through traditional farming over an outdoor space in natural environments, a growing number of farmers are beginning to embrace modern, vertical farming. Vertical farming is the practice of growing plants in vertically stacked layers. It’s typically done indoors and is highly automated. This provides several benefits:
Futura Automation offers a range of solutions for automated manufacturing. The principles of manufacturing – high quality and repetitive, efficient production – can be applied to agriculture. It is possible today to robotically plant, grow and harvest fresh vegetables close to the consumers, even in large cities. This is done with “vertical farms” that are built in warehouse spaces as tall as 40 feet. Specialized robots, known as Automated Storage and Retrieval Systems (ASRS for short) are used to efficiently access rows of crops stacked on top of each other. All can be lighted through high efficiency LED lights that are optimized in the photo spectrum for plant growth.
- For high-value crops, security can be a concern. With the right tools, growers can leverage indoor spaces to limit their exposure to risk.
- Automated systems vastly improve the yield and quality of crops.
- Reducing the investment in manual labor facilitates leaner operations that are optimized for profitability.
Using vertical farming technology for efficient automation
Many growers use HVAC (heating, ventilation, and air conditioning) and building controls to maintain tight regulation of the environmental temperature, humidity, carbon dioxide, oxygen, and light, as well as systems that care for the plants managing nutrient delivery, watering cycles, and other factors that change with plant growth phases. Understandably, the sophisticated equipment required to manage and tend to the plants can be costly.
That’s why some operators that don’t want to buy (or can’t afford) 20 or 30 systems to service stationary rows of plants instead employ vertical farming composed of movable walls that enter and exit stations serviced by one sophisticated robot that executes several plant-management tasks.
In these operations, rack walls filled with growing plants roll into and out of one or two automated stations for servicing. Cartesian robots at these stations execute various jobs. One function of a Cartesian robot might be to move a vision system around the plants to visually inspect for health and quality — and even track states of growth or collect images for analysis. Other functions might be to move a sampling array around the plants to verify pH levels or to take a trimmer around the plants for pruning.
This design concept borrows from the design of automatic storage and retrieval systems (AS/RS), an industry where Cartesian robots have often been employed. In this use-case, this concept services a living X-Y-Z matrices — using many of the same servomotor-driven gantry designs.
Like AS/RS, vertical farming necessitates linear motion designs capable of long travel distances — as much as 12 to 15 feet wide to 15 feet tall for some vertical farming walls. In addition to wide span capabilities, these systems also need to be able to manage heavy payloads, especially if they will be transporting water. Macron’s versatile Linear Robots are ideally suited for these tasks.
Recent Comments