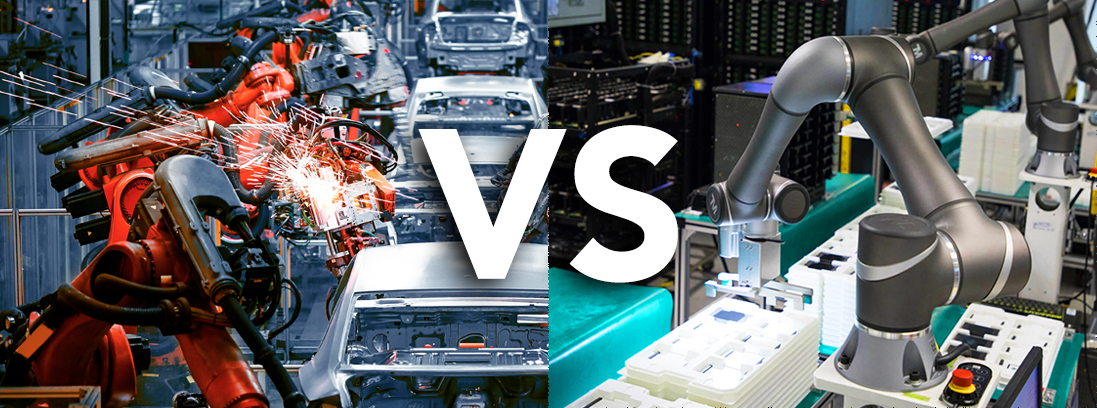
Cobot vs Robot in Assembly
Industrial Robot Strengths:
Speed – industrial robots are built for speed and repetition. A big part of a robot cell cost justification versus humans is the ability to manufacture more products in the same period of time, ideally, with higher quality. But speed requires the mass to maintain arm rigidity over time which introduces mechanical inertia. With higher inertia comes the chance for the robot arm, with its payload, to impart more physical harm to a human. Therefore, industrial robots are a safety risk and must be protected against harming workers.
Repeatability – as mentioned industrial robots have heavier and more rigid components than their cobot brethren. Many of the components are cast steel and end of arm is often finished with CNC-grade tooling for high precision gripping. This is to achieve high repeatability and long life at high accel and decel velocity profiles for precise assembly applications such as electronic circuits or medical devices.
Topologies – as industrial robots have been on the market for 50+ years now, they have evolved into a wide range of topologies to match the manufacturing requirement. There are four primary robot topologies: SCARA (4 axis) like Denso Robotics, Delta (3 or 4 axis) such as AEMK, Cartesian (3 or 4 axis) like Macron Dynamics and Articulated (5 or 6 axis) like Fanuc Robotics. This wide range of topological / kinematic options along with various reach and payloads allows for industrial robots to be optimized for the task required. SCARA robots are especially suitable for precise tasks due to fewer axes and less required reach
Price – surprisingly, industrial robots with their heavier cast frames, larger drives for torque to move those large frames fast, are lower priced than the equivalent payload and reach of a cobot. This is probably due to economies of scale and competition. But overall solutions will often be lower priced, even including safety systems required by industrial robots
Collaborative Robot (Cobot) Strengths:
Flexibility – cobots, such as Fanuc, Omron TM or Aubo, can be applied in a wider range of applications than robots due to the absence of safety systems. The inherent ease of teaching a robot its moves by manually moving the tool to position allow for more teaching iterations in a period of time to trouble-shoot a new application as compared to traditional robots requiring coordinate locations.
Ease of Use – is as much due to the newness of cobot technology rather than some inherent technical advantage. Cobots have evolved only in the past 8-10 years. As such, they were not held back by legacy systems where programming is concerned. The newest cobots have very intuitive programming software including the “touch and click” teaching techniques. This makes their application by non-technicians simpler and faster to learn than traditional CNC based robot programming systems. Again, because of the newness of the operating system, some cobot companies have also followed Apple’s iPhone lead and created simple serial interfaces for peripheral devices like grippers and vision: a cobot “ecosystem”
Inherent Safety – cobots, operated within their speed and load limits, are inherently safe by global risk standards like ISO 10218 parts 1 and 2. This allows their use without any guarding or additional safety strategies. This is very good as it lowers system cost. However it also decreases system performance. The one thing customers want from their cobot / robot is higher speeds than can be achieved by humans doing the same task. Some tasks, like test and inspection or machine tending do not require high speed. These are the best applications for cobots. Cobots can be programmed for speed but at that point safety systems must be installed and the ease of use and lower peripherals cost advantages are lost.
Recent Comments