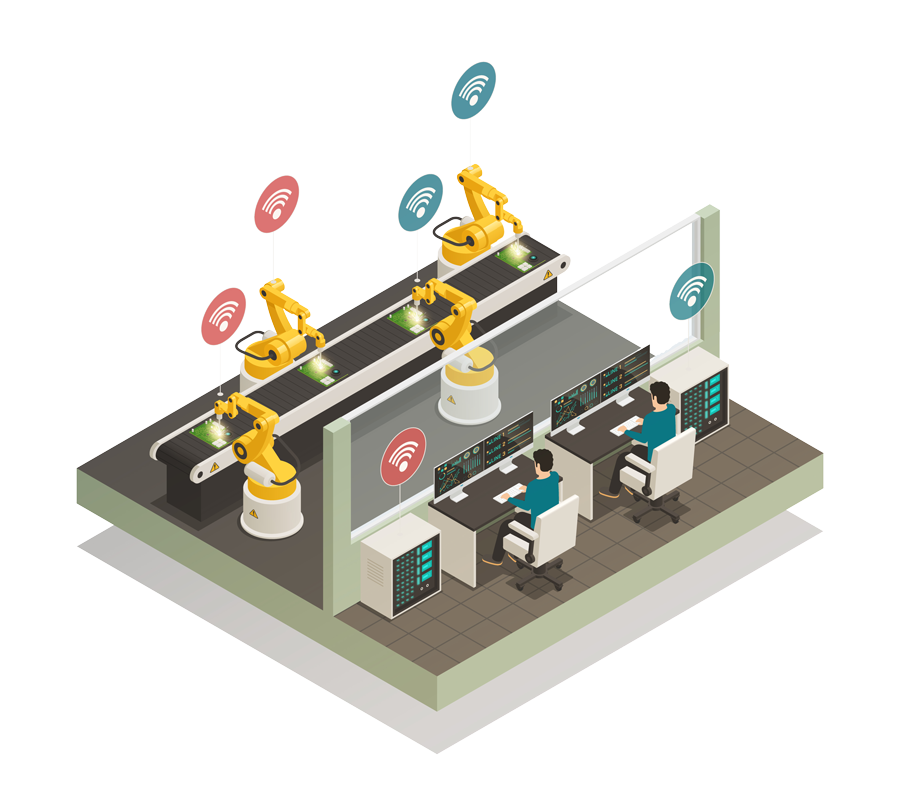
How can we reduce waste and become more lean? One way is to identify losses around a robot cell operation. A manager once said “You can never recover lost robot cell time”.
Goal: minimize idle robot cell time
How do we capture losses?
How do we categorize those losses?
How do we put that process in the path of the worker?
How do we prevent pencil whipping a log?
How do we classify varied hand written explanations?
Solution: Use IIoT to aid your monitoring process
Use the OPC-UA tags available on your legacy robot cell controller
Use a Tulip OPC-UA micro server to share the machine state
Use Tend.ai platform or PLC such as Weintek cMT3072 to convert machine inputs to OPC-UA tags
Click on the image below to see an animation of and idealized implementation
Use Tend.ai platform or PLC suchas Weintek cMT3072 to convert machine inputs to OPC-UA tags
Use Tulip to prompt the operator to identify the reason the robot cell stopped
Use an output on the OPC-UA gateway or PLC to not release an inhibit run until the reason code has been entered
To avoid capturing losses for 2 second peaks in the door, set a timer, so the prompt won’t happen until an unacceptable time has passed.
With Tulip you can pareto the losses remotely
Recent Comments