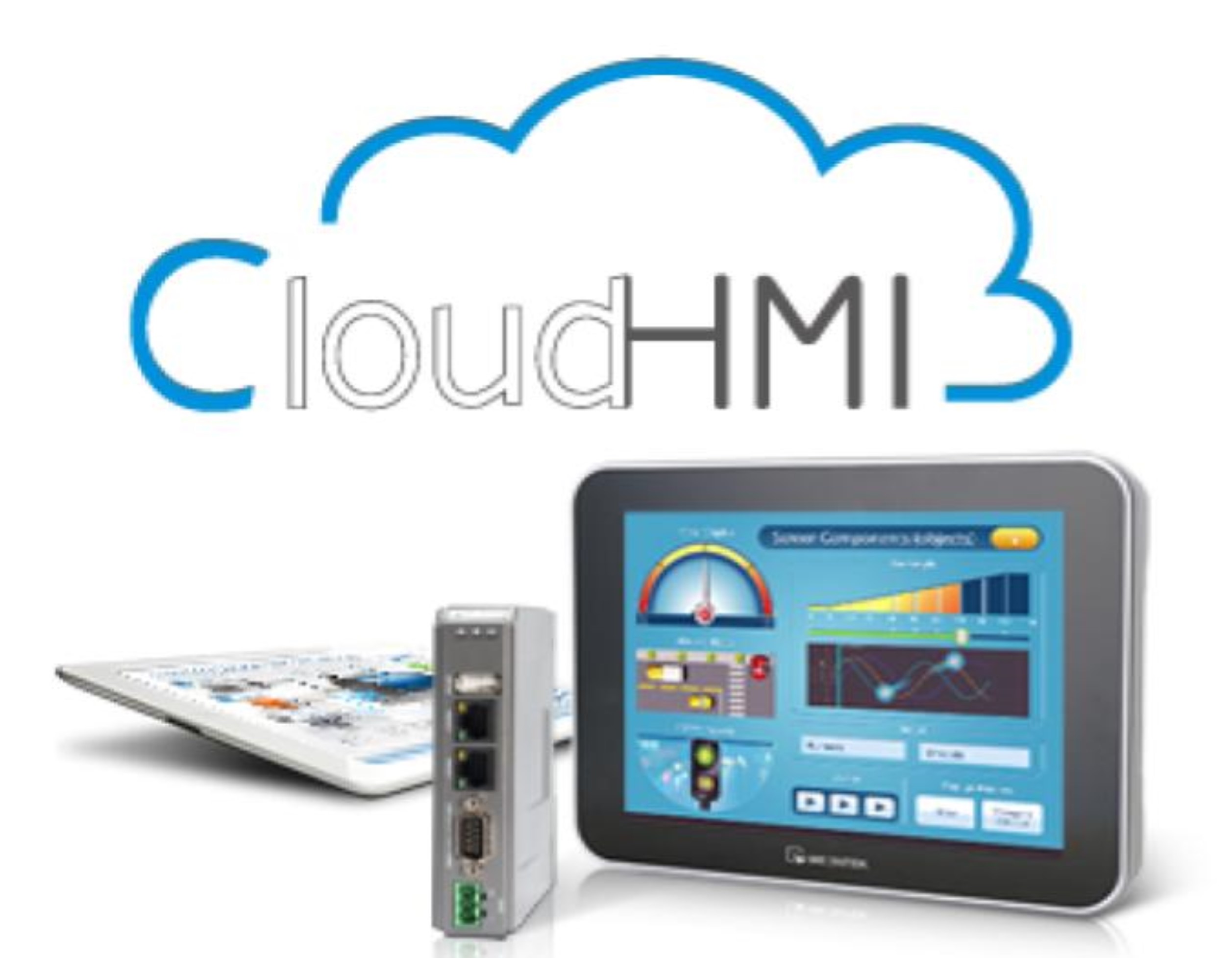
OEE (Overall Equipment Effectiveness) is the gold standard for measuring manufacturing productivity. Simply put – it identifies the percentage of manufacturing time that is truly productive. An OEE score of 100% means you are manufacturing only Good Parts, as fast as possible, with no Stop Time. In the language of OEE that means 100% Quality (only Good Parts), 100% Performance (as fast as possible), and 100% Availability (no Stop Time).
Measuring OEE is a manufacturing best practice. By measuring OEE and the underlying losses, you will gain important insights on how to systematically improve your manufacturing process. OEE is the single best metric for identifying losses, benchmarking progress, and improving the productivity of manufacturing equipment (i.e., eliminating waste).
https://www.oee.com/
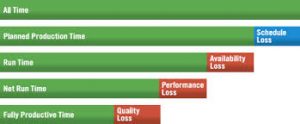
OEE is a perfect fit within the concept of Industry 4.0. It is the metric that measures the effectiveness of implementation of Industry 4.0 philosophies, which as we have said in the past include:
- Real-time Condition Monitoring. Your machines and sensor data are recorded and displayed in real time, providing the basis for real-time condition monitoring. Data visualization will not be restricted to the control station (but will be available on remote handheld devices / PDAs). The same solution is available everywhere, using big screens, smart devices like tablets, smartphones or even smart watches. This will be on the premises or in the cloud and accessed by predetermined people, including experts and technicians. No user license will ensures that you maximize the benefits of our support.
- Flexible Evaluation & Analysis Options. Intuitively presented software solutions allow you to use highly customized, predefined rules and analyse Production planners, process experts, and even maintenance technicians will be able to configure, on their own, without need of complicated IT know-how. Software is designed for human needs and not with the machine on mind, so software adapts to the users’ particular needs. The maintenance technician can create rules, like pre-defined machine parameters, that trigger notice of upcoming maintenance in the form of texts, messages or emails. This will result in maintenance performed only when it is actually needed. You will be able to set limited values and rules, so unscheduled machine stoppages will be immediately displayed and notifications will be sent to the relevant people. All in real-time.
- Targeted Notifications are generated by the system and sent to experts instantly, as soon as the software solution identifies an upcoming maintenance task, based on pre-set parameters. This information is directed only to people you want to receive it. When an issue has been addressed, relevant information is noted for the task performed, so maintenance technicians can have instant access. Each technician has a smart device, tablet or smart phone, which is intuitively presenting overviews and status of maintenance they have done or are currently performing. Experts in the plant continuously improve the maintenance cycle. Maintenance technicians continue to tweak the condition monitoring parameters as time goes by and also add new parameters. In the case of a technician’s being on sick leave, the knowledge library of maintenance and repair notifies and instructs the replacement technician. He/she only have to follow set instruction, which results in reduced training and HR flexibility. Information are constantly expanded and updated or shared, leading to a continual improvement in repair times.
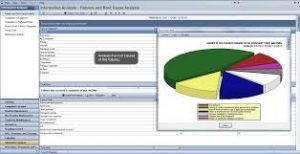
According to Wikipedia: Overall equipment effectiveness (OEE) is a term coined by Seiichi Nakajima[1] in the 1960s to evaluate how effectively a manufacturing operation is utilized. The results are stated in a generic form which allows comparison between manufacturing units in differing industries. It is not however an absolute measure and is best used to identify scope for process performance improvement, and how to get the improvement.[2] If for example the cycle time is reduced, the OEE will increase i.e. more product is produced for less resource. Another example is if one enterprise serves a high volume, low variety market, and another enterprise serves a low volume, high variety market. More changeovers (set-ups) will lower the OEE in comparison, but if the product is sold at a premium, there could be more margin with a lower OEE.
OEE measurement is also commonly used as a key performance indicator (KPI) in conjunction with lean manufacturing efforts to provide an indicator of success. OEE can be illustrated by a brief discussion of the six metrics that comprise the system. The hierarchy consists of two top-level measures and four underlying measures.
Please contact Futura Automation for more information on how we can help you maximize your OEE.
Recent Comments