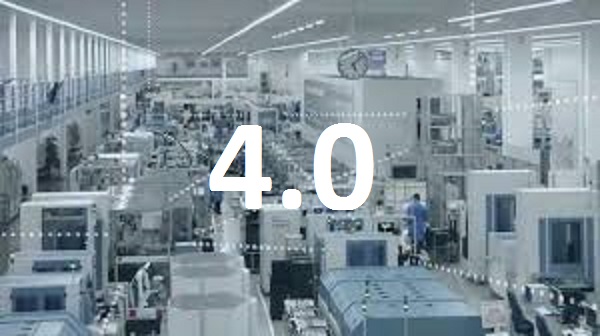
Industry 4.0 is a name for the current trend of automation and data exchange in manufacturing technologies. It is also know as the Smart Factory or “Lights-out Manufacturing”. It includes cyber-physical systems, the Internet of things, cloud computing[1[2][3][4] and cognitive computing. Artificial Intelligence (AI) plays a large role in executing the smart factory as do industrial robots and autonomous mobile robots, which are often referred to as SLAM technology. The term was developed by the Deutsch (German) government and launched at Hanover Fair 2011 through a working group (WG).
Industry 4.0 is the next stage of the industrial revolution which began with the invention of the printing press or the cotton gin, depending on sources. Industry 1.0 was Steam Power (1700) and other forms of water-driven factory mechanization (Line-shaft driven machinery) such as textile looms; Industry 2.0 was Electrification, Telecommunication and the Combustion Engine (1880) and also the advent of assembly lines; Industry 3.0 was the Computer era circa (1950), accompanied by Robotics and Automation, culminating with wide availability of the Internet and wireless devices; Industry 4.0 will be the era where machines talk to machines directly (M2M) and remotely via Cloud communications and storage. Basic AI (artificial intelligence) will begin to be applied to analyze machinery failure patterns so that maintenance can be anticipated. Industry 4.0 has also been called “The Fourth Industrial Revolution” by Klaus Schwab. It certainly is and will be all of that as it changes the way people work and the amount of work available to basic manufacturing laborers.
As the author of this paper, I will speculate that Industry 5.0 will begin around (2040) and will be the era where machines build and repair machines so that manufacturing itself becomes autonomous. Production costs will be driven towards $0 for all goods as is the trend today for highly automated consumer electronics production. Lower cost and higher quality will continue to drive the automation trend.
Now that we understand the basic definition of Industry 4.0, what will it do for global manufacturing? The basic promise of the Smart Factory was outlined very effectively by the original Deutsche Working Group that developed the concept and named it. This group defined four basic tenets of Industry 4.0. From the Wiki page for Industry 4.0:
There are four design principles in Industry 4.0. These principles support companies in identifying and implementing Industry 4.0 scenarios.[1]
- Interoperability: The ability of machines, devices, sensors, and people to connect and communicate with each other via the Internet of Things (IoT) or the Internet of People (IoP)
- Adding IoT will further automate the process to a large extent[9]
- Information transparency: The ability of information systems to create a virtual copy of the physical world by enriching digital plant models with sensor data. This requires the aggregation of raw sensor data to higher-value context information.
- Technical assistance: First, the ability of assistance systems to support humans by aggregating and visualizing information comprehensibly for making informed decisions and solving urgent problems on short notice. Second, the ability of cyber physical systems to physically support humans by conducting a range of tasks that are unpleasant, too exhausting, or unsafe for their human co-workers.
- Decentralized decisions: The ability of cyber physical systems to make decisions on their own and to perform their tasks as autonomously as possible. Only in the case of exceptions, interferences, or conflicting goals, are tasks delegated to a higher level.
To examine the first, and perhaps most critical of these design principles, we can look at Interoperability. This is the equivalent of unifying machine language, tearing down the Tower of Babel that are the myriad protocols and transport mediums which make connecting and sharing machine information almost impossible today. There are a very large range of machines that need connection to each other and to people, around the world and in the language of all the various people’s of the world that will interact with the machinery.
There are literally hundreds of different machines to link and coordinate in a typical manufacturing facility. They most likely have different brands and models of control, if the machine even has electronic control. There are different types of control for machine tools (CNCs), stamping and rolling presses, injection molders and extrusion machines, casting machines, conveyors, wrappers, stackers, sorting, picking, baking, freezing, inspection, packaging and labeling machines and robots, both fixed and mobile. For each type of machine, there are dozens of control solutions. Most of the controllers do not communicate using the same protocol or language, if they are even equipped to communicate at all. For Industry 4.0 dreams to be realized, all machines must talk to each other and they must talk be able to communicate in the same language or have a real-time translator do that for the machine controller.
There are almost as many controller languages and protocols as there are controller models. RS232, RS485, HART, MELSECnet, MODBUS 485 and TCP, CC-Link, DF-1, DeviceNet and ControlNet, Profibus and Profinet, Ethernet IP and EtherCat, Sercos, and many more. Here is a complete list on this link.
So how do all these devices, speaking so many languages communicate to each other and with human operators? There are a number of industrial translation products including Kepware. The best of these devices today seems to be Weintek cMT series of translators and HMIs with integrated translation. Such translators will convert the native communication protocol to a standardized protocol that can be transmitted by hard-wire MODBUS Ethernet communications, by WiFi within a facility or can be sent to a Cloud service application, EasyAccess 2.0 in the case of Weintek, for distribution anywhere in the world. The data can be delivered for human interaction and response to desktop PC or servers within another facility or to IOS, Windows OS or Android handheld devices like Apple iPhone, Microsoft Surface or Samsung Galaxy devices.
How does Industry 4.0 and the Smart Factory then benefit manufacturing? It contributes in many ways to reduce cost, improve quality and increase production. Here are the key economic or business drivers derived from Industry 4.0:
- Reduced Labor and Maintenance Costs
- as machine monitoring and repair activities are concentrated to fewer and more expert hands and in real-time, maintenance becomes more predictive in nature and less reactive
- as machines provide greater throughput due to additional up-time, production increases for unit of labor
- with the development of a manufacturing infrastructure that more effectively supports robotics and advanced automation such as additive manufacturing, further reducing unit labor costs
- fewer quality problems lead to less material waste, lower personnel and operating costs.
- the speed and ability to handle a high product mix seamlessly will also lower changeover costs.
- Greater Revenues
- from lower costed and so potentially lower priced products and/or greater manufacturing margins
- from better product availability and delivery from additional machinery up-time and coordination
- puts manufacturers on a path to be a preferred supplier to current customers
- opens up ways to serve larger markets
- offer customized and thus higher-margin products
- with intelligent products and operations the ability to offer key services to accompany products
- Improved Efficiency
- as machines are tightly interconnected and so less time with work-in-process
- with fewer people and more automation, companies can make decisions more rapidly and keep efficiency high
- automation also tends to keep quality high due to repeatability of machines, backed by vision systems for inline 100% inspection
- Inherent Agility
- with the massive data available from multiple machines that are interconnected
- permits a marketing focus on high mix, small lots, and even one-off manufacturing
- when products know their own manufacturing specifications via Smart Factory, it accelerates processes throughout production
- Increased Innovation
- with faster feedback from customers and manufacturing processes providing product design insights
- since Industry 4.0 production lines are made to accommodate high mix and low volumes, they are ideally suited to new product introduction and experimentation in design.
- extreme visibility from IIoT sensor feeds to intelligent products and equipment enables deeper understanding of what works in both product and process design
- Maximized Customer Experience
- customer self-service views into the production operation may be possible; watch your product as it is manufactured
- detailed, yet in-context, data from MES can be a foundation for quickly resolving issues between customers and manufacturer
- customized products
- high product and service quality
- great prices
- fast delivery
Credit for identifying the above business drivers goes to Francisco Almada-Lobo. He is a MESA (Manufacturing Enterprise Solutions Association) Member and CEO of Critical Manufacturing. The article from which these drivers are cited originally appeared on MESA International’s blog.
It might be possible for a typical SME (Small to Medium Manufacturer) to achieve the same types of workplace efficiency as its Fortune 500 competitors through implementation of Industry 4.0 principles and practices. Let’s take a look at one area of opportunity with Industry 4.0 and the “Reduced Costs” driver to help maintain production machinery up-time, predictive analytics. From Xintrix we learn the following three benefits:
- Real-time Condition Monitoring. Your machines and sensor data are recorded and displayed in real time, providing the basis for real-time condition monitoring. Data visualization will not be restricted to the control station (but will be available on remote handheld devices / PDAs). The same solution is available everywhere, using big screens, smart devices like tablets, smartphones or even smart watches. This will be on the premises or in the cloud and accessed by predetermined people, including experts and technicians. No user license will ensures that you maximize the benefits of our support.
- Flexible Evaluation & Analysis Options. Intuitively presented software solutions allow you to use highly customized, predefined rules and analyse Production planners, process experts, and even maintenance technicians will be able to configure, on their own, without need of complicated IT know-how. Software is designed for human needs and not with the machine on mind, so software adapts to the users’ particular needs. The maintenance technician can create rules, like pre-defined machine parameters, that trigger notice of upcoming maintenance in the form of texts, messages or emails. This will result in maintenance performed only when it is actually needed. You will be able to set limited values and rules, so unscheduled machine stoppages will be immediately displayed and notifications will be sent to the relevant people. All in real-time.
- Targeted Notifications are generated by the system and sent to experts instantly, as soon as the software solution identifies an upcoming maintenance task, based on pre-set parameters. This information is directed only to people you want to receive it. When an issue has been addressed, relevant information is noted for the task performed, so maintenance technicians can have instant access. Each technician has a smart device, tablet or smart phone, which is intuitively presenting overviews and status of maintenance they have done or are currently performing. Experts in the plant continuously improve the maintenance cycle. Maintenance technicians continue to tweak the condition monitoring parameters as time goes by and also add new parameters. In the case of a technician’s being on sick leave, the knowledge library of maintenance and repair notifies and instructs the replacement technician. He/she only have to follow set instruction, which results in reduced training and HR flexibility. Information are constantly expanded and updated or shared, leading to a continual improvement in repair times.
Futura Automation, LLC would like to offer its experience and capability in helping manufacturers evaluate and implement Industry 4.0 practices. Futura Automation is uniquely positioned through the skillsets of its partners to assist its clients in utilizing these philosophies to achieve business success in the 21st century.
Recent Comments