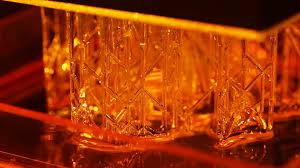
Check out Futura Automation’s Quik Jig 3D Printing services: www.futura-automation.com/partners/quik-jig
3D Printing is becoming “main stream”. This technology has advanced from a cutting edge product development tool, especially in the automotive industry, in the 1990s, to a dependable form of mass customization and production for plastic, metal and even organic products and parts.
The 3D printing process builds a three-dimensional object from a computer-aided design (CAD) model, usually by successively adding material layer by layer, which is why it is also called additive manufacturing, unlike conventional machining, casting and forging processes, where material is removed from a stock item (subtractive manufacturing) or poured into a mold and shaped by means of dies, molds, presses and hammers.
Futura Automation LLC is focused on the industrial market for custom and low volume part manufacturing in a wide variety of materials. Futura Automation assists clients in achieving higher efficiencies and better quality in low run component manufacturing primarily through support in robot and automation implementation. 3D printing is another technology that is important to the future of high mix and low volume manufacturing. Futura Automation will assist its clients with implementation of 3D printing technologies. The following is an overview of the market, with reference help from Wikipedia.
The main differences between 3D printing processes are in the way layers are deposited to create parts and in the materials that are used. Each method has its own advantages and drawbacks, which is why some companies offer a choice of metal powder or polymer for the material used to build the object. The main considerations in choosing a machine are generally speed, cost of the 3D printer, of the printed prototype, choice, strength, flexibility, temperature resistance and cost of the materials, and color capabilities. Printers that work directly with metals are generally expensive. However, less expensive printers can be used to make a sacrificial mold, which is then used to make metal parts and is destroyed in the process of production.
ISO/ASTM52900-15 defines seven categories of Additive Manufacturing (AM) processes (expanded here to more current techniques as outlined in AMSC https://share.ansi.org/Shared%20Documents/Standards%20Activities/AMSC/AMSC_Roadmap_June_2018.pdf):
- material extrusion
- fused filament fabrication (FFF)
- filament deposition (FDM)
- binder jetting (BJ)
- laminated object manufacturing (LOM)
- material jetting (MJ)
- directed energy deposition (DED)
- digital light processing (DLP)
- stereo-lithography (SLA)
- powder bed fusion (PBF)
- selective laser sintering (SLS)
- selective laser melting (SLM)
- electron beam melting (EBM)
- vat polymerization (VP)
As of December 2017, additive manufacturing systems were on the market that ranged from $99 to $500,000 in price and were employed in industries including aerospace, architecture, automotive, defense, and medical replacements, among many others. For example, General Electric uses high-end 3D Printers to build parts for turbines. Many of these systems are used for rapid prototyping, before mass production methods are employed.
Material Extrusion (ME)
Some of the early and low-cost methods of 3D printing melted or softened the polymer material to produce the layers. It is also called extrusion. In fused filament fabrication (FFF), also known as fused deposition modeling (FDM), the model or part is produced by extruding small beads or streams of material which harden immediately to form layers. A filament of thermoplastic, metal wire, or other material is fed into an extrusion nozzle head (3D printer extruder), which heats the material and turns the flow on and off. FDM is somewhat restricted in the variation of shapes that may be fabricated. Another technique fuses parts of the layer and then moves upward in the working area, adding another layer of granules and repeating the process until the piece has built up. This process uses the unfused media to support overhangs and thin walls in the part being produced, which reduces the need for temporary auxiliary supports for the piece. Recently, FFF/FDM has expanded to 3D print directly from pellets to avoid the conversion to filament. This process is called fused particle fabrication (FPF) (or fused granular fabrication (FGF) and has the potential to use more recycled materials. Futura Automation is not participating in the FFF and FDM methods at this point in time as it is primarily for low quality prototyping and hobbyists.
Some industrial FFF / FDM printers include: Prusa i3, Stratasys,
Binder Jetting (BJ)
BJ is a 3D printing process that uses two types of materials to build objects: a powder-based material (usually gypsum) and a bonding agent. As the name suggests, the “bonding” agent acts as a strong adhesive to attach (bond) the powder layers together. The printer nozzles extrude the binder in liquid form similar to a regular 2D inkjet printer. After completing each layer, the build plate lowers slightly to allow for the next one. This process repeats until the object reaches its required height.
The four popular materials used in BJ printing include:
- Ceramics
- Metals
- Sand
- Plastics
It’s not possible to get super high-resolution or overly rugged 3D objects with BJ printing, but there are other advantages. For example, these printers allow you to print parts in full color. To do this, you simply add color pigments to the binder, which typically include black, white, cyan, yellow, and magenta. This technology is still advancing, so expect more great things to come in the future. At the time of writing, some applications of BJ 3D printing include rapid prototyping, and various uses in the aerospace, automotive, and medical industries.
Some BJ printers include: Addwii Unveils The X1, ExOne R2, ZCorp Spectrum z510
Laminated Object Manufacturing (LOM)
A Californian company called Helisys Inc. (now Cubic Technologies), first developed LOM as an effective and affordable method of 3D printing. A US design engineer named Michael Feygin—a pioneer in 3D printed technologies—originally patented LOM. LOM is a rapid prototyping system that works by fusing or laminating layers of plastic or paper using both heat and pressure. A computer-controlled blade or laser cuts the object to the desired shape. Once each printed layer is complete, the platform moves down by about 1/16th of an inch, ready for the next layer. The printer then pulls a new sheet of material across the substrate where it’s adhered by a heated roller. This basic process continues over and over until the 3D part is complete.
One popular LOM printer is: The Mcor Matrix
Material Jetting (MJ)
Material Jetting is referred to as wax casting. Unlike other 3D printing technologies, there isn’t a single inventor for MJ. In fact, up until recent times it’s been more of a technique than an actual printing process. It’s something jewelers have used for centuries. Wax casting has been a traditional process where the user produces high-quality, customizable jewelry. The reason it gets a mention here is because of the introduction of 3D printing. Thanks to the arrival of this technology, wax casting is now an automated process. Today, MJ 3D printers produce high-resolution parts, mainly for the dental and Jewelry industries,
For jewelers who want to experiment with various casts—as most jewelers do—MJ is now their leading 3D technology. At the time of writing, there are a few high-quality professional wax 3D printers on the market. Here’s how they work:
Once the 3D model (CAD file) is uploaded to the printer, it’s all systems go. The printer adds molten (heated) wax to the aluminum build platform in controlled layers. It achieves this using nozzles that sweep evenly across the build area. As soon as the heated material lands on the build plate it begins to cool down and solidify (UV light helps to cure the layers). As the 3D part builds up, a gel-like material helps to support the printing process of more complex geometries. Like all support materials in 3D printing, it’s easy to remove it afterward, either by hand or by using powerful water jets. Once the part is complete you can use it right away, no further post-curing necessary.
There are also Polyjet MJ 3D printers, which use photo-polymer resins rather than synthetic waxes. Polyjet technology also offers very good resolution. Unlike digital wax printers, people use Polyjet devices to create parts for a wide range of industries.
HP has developed the Multi Jet Fusion (MJF) which is a powder base technique, though no laser are involved. An inkjet array applies fusing and detailing agents which are then combined by heating to create a solid layer.
Some MJ printers include: ABS 3D printer, PLA 3D printer (large format), HP Multi Jet Fusion
Digital Light Processing (DLP)
DLP is the oldest of the 3D printing technologies, created by a man called Larry Hornbeck back in 1987. It’s similar to SLA (see below), given that it also works with photopolymers. The liquid plastic resin used by the printer goes into a translucent resin container. There is, however, one major difference between the two, which is the source of light. While SLA uses UV (ultra-violet) light, DLP uses a more traditional light source, usually arc lamps. DLP can be used to quickly fabricate photopolymer parts. These printers work in the same way as SLA, but replace the actuated laser with a projector that can cure an entire layer at once. This process results in pretty impressive printing speeds. When there’s plenty of light, the resin is quick to harden (we’re talking seconds). Compared to SLA 3D printing, DLP achieves quicker print times for most parts. The reason it’s faster is because it exposes entire layers at once. With SLA printing, a laser has to draw out each of these layers, and this takes time.
In the case of “Carbon 3D” parts printed with Digital Light Synthesis™ are much more like injection-molded parts. Digital Light Synthesis™ produces consistent and predictable mechanical properties, creating parts that are solid on the inside. Digital Light Synthesis™ technology is driven by Carbon’s groundbreaking CLIP™ process and programmable liquid resins. CLIP™ uses digital light projection in combination with oxygen permeable optics. Traditional additive approaches to photo polymerization typically produce weak, brittle parts. Carbon overcomes this by embedding a second heat-activated programmable chemistry in their materials. This results in high-resolution parts with engineering-grade mechanical properties
Some DLP printers include: Makex M-one Desktop DLP 3d Printer, Desktop UV DLP, LumiPocket – Miniature DLP, Solus DLP 3D Printer; Carbon 3D (Digital Light Synthesis)
Stero-Lithography (SLA)
A key technology in 3D printing is stereo-lithography. This is the foundational technique for 3D printing and is commonly called SLA. SLA is a fast prototyping process. Those who use this technology are serious about accuracy and precision. It can produce objects from 3D CAD data (computer-generated) files in just a few hours. This is a 3D printing process that’s popular for its fine details and exactness. Machines that use this technology produce unique models, patterns, prototypes, and various production parts. They do this by converting liquid photopolymers (a special type of plastic) into solid 3D objects, one layer at a time. The plastic is first heated to turn it into a semi-liquid form, and then it hardens on contact. The printer constructs each of these layers using an ultra-violet (UV) laser, directed by X and Y scanning mirrors. Just before each print cycle, a recoater blade moves across the surface to ensure each thin layer of resin spreads evenly across the object. The print cycle continues in this way, building 3D objects from the bottom up.
Once completed, someone takes the 3D object from the printer and detaches it carefully from the platform. The 3D part will usually have a chemical bath to remove any excess resin. It’s also common practice to post-cure the object in an ultra violet oven. What this does is render the finished item stronger and more stable. Depending on the part, it may then go through a hand sanding process and have some professional painting done. SLA printing has become a favored economical choice for a wide variety of industries. Some of these include automotive, medical, aerospace, entertainment, and also to create various consumer products.
Futura Automation is partnering with FormLabs on the SLA and SLS techniques for printing. Formlabs 2 machines are SLA based technology. The new Formlabs 3 and 3L are a new technique called Low Force Stereo-lithography (LFS) which provides better resolution and larger shapes. The new Formlabs Focus 1 uses SLS technology for metal part production. With stereo-lithography techniques, there is material left loose that requires removal. Formlabs also has a solution for this task which is called Form Wash and Form Cure which allows for post-processing of SLA printed parts.
The reverse of liquid bath systems like Formlabs are Inkjet printer systems like the “Objet” PolyJet system by Stratsys spray photo-polymer materials onto a build tray in ultra-thin layers (between 16 and 30 µm) until the part is completed. Each photo-polymer layer is cured with UV light after it is jetted, producing fully cured models that can be handled and used immediately, without post-curing. Ultra-small features can be made with the 3D micro-fabrication technique used in multi-photon photo-polymerization. Due to the nonlinear nature of photo excitation, the gel is cured to a solid only in the places where the laser was focused while the remaining gel is then washed away. Feature sizes of under 100nm are easily produced, as well as complex structures with moving and interlocked parts. Yet another approach uses a synthetic resin that is solidified using LEDs.
Some SLA printers include: 3D printer Pegasus Touch SLA technology, XYZprinting Nobel 1.0 SLA 3D Printer, SUNLU SLA Desktop 3D Printer, Form 2 + SLA 3D Printer,
Powder Bed Fusion (PBF)
PBF, include several processes such as DMLS, SLS, SLM, MJF and EBM. Powder Bed Fusion processes can be used with an array of materials and their flexibility allows for geometrically complex structures, making it a go-to choice for many 3D printing projects. These techniques include selective laser sintering (SLS), with both metals and polymers, and direct metal laser sintering (DMLS). Selective laser melting does not use sintering for the fusion of powder granules but will completely melt the powder using a high-energy laser to create fully dense materials in a layer-wise method that has mechanical properties similar to those of conventional manufactured metals. Electron beam melting (EBM) is a similar type of additive manufacturing technology for metal parts (e.g. titanium alloys). EBM manufactures parts by melting metal powder layer by layer with an electron beam in a high vacuum..
Some PBF printers include: EOS M400 Quad, Additive Industries MetalFab1, Realizer, TrumpTruprint, SLM Solutions, XACT Metal
Selective Laser Modeling (SLM)
SLM made its debut appearance back in 1995. It was part of a German research project at the Fraunhofer Institute ILT, located in the country’s most western city of Aachen. Like SLA (see above), SLM also uses a high-powered laser beam to form 3D parts. During the printing process, the laser beam melts and fuses various metallic powders together. The simple way to look at this is to break down the basic process like thus:
Powdered material + heat + precision + layered structure = a perfect 3D object.
As the laser beam hits a thin layer of the material, it selectively joins or welds the particles together. After one complete print cycle, the printer adds a new layer of powdered material to the previous one. The object then lowers by the precise amount of the thickness of a single layer. When the print process is complete, someone will manually remove the unused powder from the object. The main difference between SLM and SLS is that SLM completely melts the powder, whereas SLS only partly melts it (sinters). In general, SLM end products tend to be stronger as they have fewer or no voids.
A common use for SLM printing is with 3D parts that have complex structures, geometries and thin walls. The aerospace industry uses SLM 3D printing in some of its pioneering projects. These are typically those which focus on precise, durable, lightweight parts. It’s a costly technology, though, and so not practical or popular with home users for that reason. SLM is quite widespread now among the aerospace and medical orthopedics industries. Those who invest in SLM 3D printers include researchers, universities, and metal powder developers. There are others too, who are keen to explore the full range and future potential of metal additive manufacturing in particular.
Some SLM industrial printers include: SLM Solutions SLM 125, 280, and 500, Realizer SLM 125, Optomec LENS 450, others.
Selective Laser Sintering (SLS, LMF and DMLS)
An American businessman, inventor, and teacher named Dr. Carl Deckard developed and patented SLS technology in the mid-1980s. It’s a 3D printing technique that uses high power CO2 lasers to fuse particles together. The laser sinters powdered metal materials (though it can utilize other materials too, like white nylon powder, ceramics and even glass). This technique of SLS has many variations / goes by many other names including Laser Material Fusing, Direct Metal Tooling and Direct Metal Laser Sintering.
The build platform, or bed, lowers incrementally with each successive laser scan. It’s a process that repeats one layer at a time until it reaches the object’s height. There is un-sintered support from other powders during the build process that surround and protect the model. This means the 3D objects don’t need other support structures during the build. Someone will remove the un-sintered powders manually after printing. SLS produces durable, high precision parts, and it can use a wide range of materials. It’s a perfect technology for fully-functional, end-use parts and prototypes. SLS is quite similar to SLA technology with regards to speed and quality. The main difference is with the materials, as SLS uses powdered substances, whereas SLA uses liquid resins. It’s this wide variety of available materials that makes SLA technology so popular for printing customized objects.
Some SLM industrial printers include: Formlabs 3 and 3L, EOS, Concept Laser, DMG Mori (DMLS), Matsuura, Trumpf (LMF) and Optomec (DED)
Electron beam modeling (EBM)
Electron beam modeling (EBM) is a newer technique for high resolution metal printing that was developed by ARCAM in Sweden and is now deployed in the aerospace industry and others. This is a 3D printing technology similar to SLM (see above), in that it uses a powder bed fusion technique. The difference between the two is the power source. The SLM approach above uses high-powered laser in a chamber of noble, or inert gas. EBM, on the other hand, uses a powerful electron beam in a vacuum. Aside from the power source, the remaining processes between the two are quite similar. EBM’s main use is to 3D print metal parts. Its main characteristics are its ability to achieve complex geometries with freedom of design. EBM also produces parts that are incredibly strong and dense in their makeup.
Computed axial lithography is a method for 3D printing based on computerized tomography scans to create prints in photo-curable resin. It was developed by a collaboration between the University of California, Berkeley with Lawrence Livermore National Laboratory. Unlike other methods of 3D printing it does not build models through depositing layers of material like fused deposition modeling and stereo-lithography, instead it creates objects using a series of 2D images projected onto a cylinder of resin. It is notable for its ability to build an object much more quickly than other methods using resins and the ability to embed objects within the prints
Some EBM printers include: ARCAM Q20
Markets and Applications
Futura Automation is focused on the major industries in western North America: Aerospace, Electronic Fabrication and Assembly, Food and Agriculture, Life Sciences and Medical Devices. Within those industries are many good manufacturing applications for 3D printing:
Additive Manufacturing
AM technologies found applications starting in the 1980s in product development, data visualization, rapid prototyping, and specialized manufacturing. Their expansion into production (job production, mass production, and distributed manufacturing) has been under development in the decades since. Industrial production roles for 3D printing within the metalworking industries achieved significant scale for the first time in the early 2010s. Since the start of the 21st century there has been a large growth in the sales of AM machines, and their price has dropped substantially.
Additive manufacturing’s earliest applications have been on the tool-room end of the manufacturing spectrum. For example, rapid prototyping was one of the earliest additive variants, and its mission was to reduce the lead time and cost of developing prototypes of new parts and devices, which was earlier only done with subtractive tool-room methods such as CNC milling and turning, and precision grinding, far more accurate than 3D printing with accuracy down to 0.00005″ (100nm) and creating better quality parts faster, but sometimes too expensive for low accuracy prototype parts. With technological advances in additive manufacturing, however, and the dissemination of those advances into the business world, additive methods are moving ever further into the production end of manufacturing in creative and sometimes unexpected ways. Parts that were formerly the sole province of subtractive methods can now in some cases be made more profitably via additive ones. In addition, new developments in RepRap (replicating rapid prototyping) technology allow the same device to perform both additive and subtractive manufacturing by swapping magnetic-mounted tool heads.
Agile Tooling
Agile tooling is the process of using modular means to design tooling for traditional subtractive manufacturing techniques and molds for plastics and die-casting that are produced by additive manufacturing or 3D printing methods to enable quick prototyping and responses to tooling and fixture needs. Agile tooling uses a cost-effective and high-quality method to quickly respond to customer and market needs. It can be used in hydro-forming, stamping, injection molding and other manufacturing processes.
Cloud-based Additive Manufacturing
Additive manufacturing in combination with cloud computing technologies allows decentralized and geographically independent distributed production. Cloud-based additive manufacturing refers to a service-oriented networked manufacturing model in which service consumers are able to build parts through Infrastructure-as-a-Service (IaaS), Platform-as-a-Service (PaaS), Hardware-as-a-Service (HaaS), and Software-as-a-Service (SaaS). Distributed manufacturing as such is carried out by some enterprises; there is also a services like 3D Hubs that put people needing 3D printing in contact with owners’ of printers. Some companies offer online 3D printing services to both commercial and private customers, working from 3D designs uploaded to the company website. 3D-printed designs are either shipped to the customer or picked up from the service provider.
Mass-Customization
Companies have created services where consumers can customize objects using simplified web based customization software, and order the resulting items as 3D printed unique objects. This now allows consumers to create custom cases for their mobile phones. Nokia has released the 3D designs for its case so that owners can customize their own case and have it 3D printed.
Rapid Manufacturing
Advances in RP technology have introduced materials that are appropriate for final manufacture, which has in turn introduced the possibility of directly manufacturing finished components. One advantage of 3D printing for rapid manufacturing lies in the relatively inexpensive production of small numbers of parts. This lends to the production of small run of new and replacement parts for industrial machine maintenance, including robot joints and End of Arm Tooling (EOAT) and specialized automation machinery.
Rapid manufacturing is a new method of manufacturing and many of its processes remain unproven. 3D printing is now entering the field of rapid manufacturing and was identified as a “next level” technology by many experts in a 2009 report. One of the most promising processes looks to be the adaptation of selective laser sintering (SLS), or direct metal laser sintering (DMLS) some of the better-established rapid prototyping methods.
Rapid Prototyping
Rapid prototyping is a group of techniques used to quickly fabricate a scale model of a physical part or assembly using three-dimensional computer aided design (CAD) data.
RP is used for a wide range of applications and are used to manufacture production-quality parts in relatively small numbers if desired without the typical unfavorable short-run economics. This economy has encouraged online service bureaus. Historical surveys of RP technology start with discussions of simulacra production techniques used by 19th-century sculptors. Some modern sculptors use the progeny technology to produce exhibitions. The ability to reproduce designs from a dataset has given rise to issues of rights, as it is now possible to interpolate volumetric data from one-dimensional images.
As with CNC subtractive methods, the computer-aided-design – computer-aided manufacturing CAD -CAM workflow in the traditional Rapid Prototyping process starts with the creation of geometric data, either as a 3D solid using a CAD workstation, or 2D slices using a scanning device. For Rapid prototyping this data must represent a valid geometric model; namely, one whose boundary surfaces enclose a finite volume, contain no holes exposing the interior, and do not fold back on themselves. In other words, the object must have an “inside”. The model is valid if for each point in 3D space the computer can determine uniquely whether that point lies inside, on, or outside the boundary surface of the model.
CAD post-processors will approximate the application vendors’ internal CAD geometric forms (e.g., B-splines) with a simplified mathematical form, which in turn is expressed in a specified data format which is a common feature in additive manufacturing: SLA (stereolithography) a de facto standard for transferring solid geometric models to SFF machines. To obtain the necessary motion control trajectories to drive the actual SFF, rapid prototyping, 3D printing or additive manufacturing mechanism, the prepared geometric model is typically sliced into layers, and the slices are scanned into lines (producing a “2D drawing” used to generate trajectory as in CNC’s toolpath), mimicking in reverse the layer-to-layer physical building process.
Robot and Machine Tooling
Customized end-of-arm-tooling for robot gripping, parts holding for production and other production tools can be produced quickly and in low volume for project requirements
Food
Additive manufacturing of food is being developed by squeezing out food, layer by layer, into three-dimensional objects. A large variety of foods are appropriate candidates, such as chocolate and candy, and flat foods such as crackers, pasta, and pizza. NASA has considered the versatility of the concept, awarding a contract to the Systems and Materials Research Consultancy to study the feasibility of printing food in space. NASA is also looking into the technology in order to create 3D printed food to limit food waste and to make food that are designed to fit an astronaut’s dietary needs. One of the problems with food printing is the nature of the texture of a food. For example, foods that are not strong enough to be filed are not appropriate for 3D printing.
Medical Devices
3D printing has been used to print patient-specific implanted and external devices for medical use. Successful operations include a titanium pelvis implanted into a British patient, titanium lower jaw transplanted to a Dutch patient, and a plastic tracheal splint for an American infant. The hearing aid and dental industries are expected to be the biggest areas of future development using custom 3D printing technology. In March 2014, surgeons in Swansea used 3D printed parts to rebuild the face of a motorcyclist who had been seriously injured in a road accident. Research is also being conducted on methods to bio-print replacements for lost tissue due to arthritis and cancer. Another growing application is the manufacturing of replacement prosthetics and orthotics for damaged or missing legs, arms, hands, fingers and feet.
3D printing technology can now be used to make exact replicas of organs. The printer uses images from patients’ MRI or CT scan images as a template and lays down layers of rubber or plastic.
Research and Development
Higher education(vocational schools, colleges and universities) have proven to be a major buyer of desktop and professional 3D printers which industry experts generally view as a positive indicator. Libraries around the world have also become locations to house smaller 3D printers for educational and community access. Several projects and companies are making efforts to develop affordable 3D printers for home desktop use. Much of this work has been driven by and targeted at DIY/Maker/enthusiast/early adopter communities, with additional ties to the academic and hacker communities.
Recent Comments